Chemistry
Designing the perfect surface catalyst
Learning how an aluminum compound binds to silica may pave the way to a reliable petrochemical catalyst.
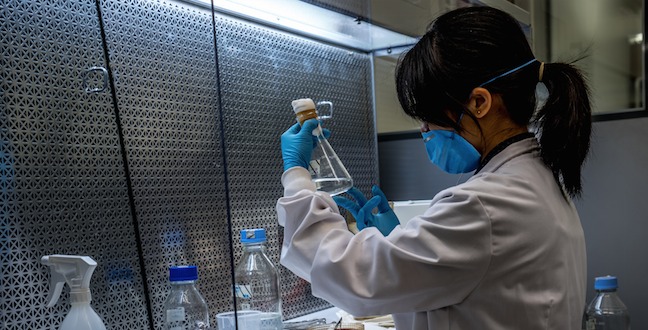
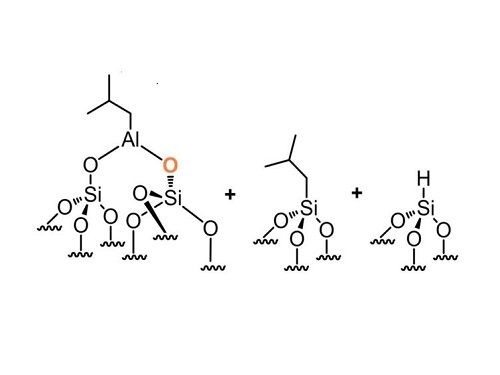
The aluminum-based compound TIBA can latch on to oxygen atoms on the surface of silica (left), but may also form unwanted side-products (center and right).
Reproduced with permission© 2015 Royal Society of Chemistry
A new form of solid catalyst in development by KAUST researchers could improve how hydrocarbons are processed in the petrochemical industry, and the researchers have cracked the secret to a smooth catalytic surface1.
Solid catalysts are widely used to speed up chemical reactions in liquids or gases that flow over them because they are relatively easy to separate and recover after the reaction has finished. They are known as heterogeneous catalysts because they exist in a different phase than the reactants.
The surface of a solid catalyst is covered in reactive chemical groups called active sites that temporarily latch on to the reactants. However, it can be difficult to ensure that all the active sites are identical and uniformly distributed, and solid catalysts often behave unpredictably.
“At the moment, a heterogeneous catalyst is a black box,” said Jean-Marie Basset, director of the KAUST Catalysis Center (KCC) and leader of the KCC research team.
His team is developing a solid catalyst that can rearrange and combine hydrocarbon molecules called alkanes. Their strategy involves grafting an aluminum-based compound called triisobutylaluminum (TIBA) on to porous silica particles.
Further chemical reactions would replace one of the aluminum’s isobutyl groups with a hydroxyl (OH), which could then tether highly-active catalysts containing metals such as tungsten or tantalum. TIBA’s reaction with silica was poorly understood, but Basset’s team revealed for the first time how it attaches to the surface of the particles in different ways.
Using several analytical techniques, the researchers found that TIBA’s aluminum atom bonds with oxygen atoms on the silica’s surface through two distinct reaction pathways. It can form a bridge between two oxygen atoms as the team hoped, but it can also add one of its isobutyl groups or a hydrogen atom directly to a silicon atom.
Calculations revealed the different pathways involved in forming these products, and these should help fine-tune the system to generate only the bridged aluminum species.
The researchers then showed that heating the bridged aluminum to 225 degrees Celsius under a high vacuum caused its remaining isobutyl group to rearrange. This created aluminum hydride compounds, just one chemical step away from the target hydroxyl. However, the aluminum hydride was bonded to 3, 4 or 5 oxygen atoms at various points on the silica surface, which would give each site a different reactivity.
Basset explains that his team discovered a solution to the problem that produces a uniform covering of identical catalytic sites. “We recently obtained unprecedented results that make our dream a reality!” he notes.
References
- Werghi, B., Bendjeriou-Sedjerari, A., Sofack-Kreutzer, J., Jedidi, A., Abou-Hamad, E., Cavallo, L. & Basset, J.-M. Well-defined silica supported aluminum hydride: another step towards the utopian single site dream? Chemical Science 6, 5456-5465 (2015).| article
You might also like
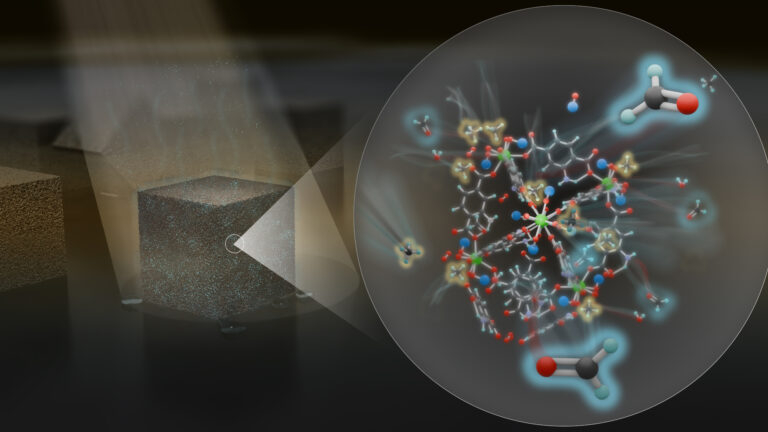
Chemistry
Maximizing methane
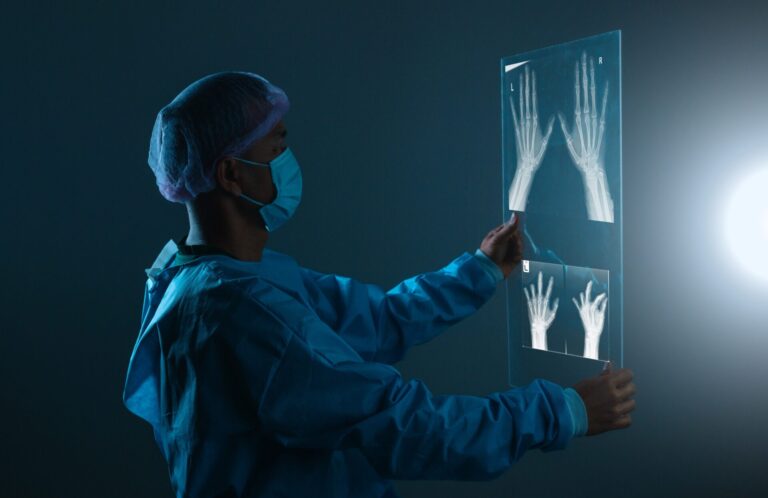
Chemistry
Beating the dark current for safer X-ray imaging
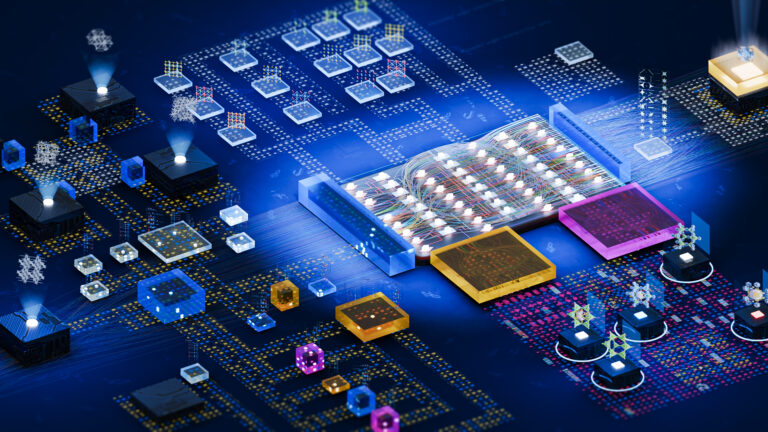
Chemical Engineering
Net benefits for advanced materials design
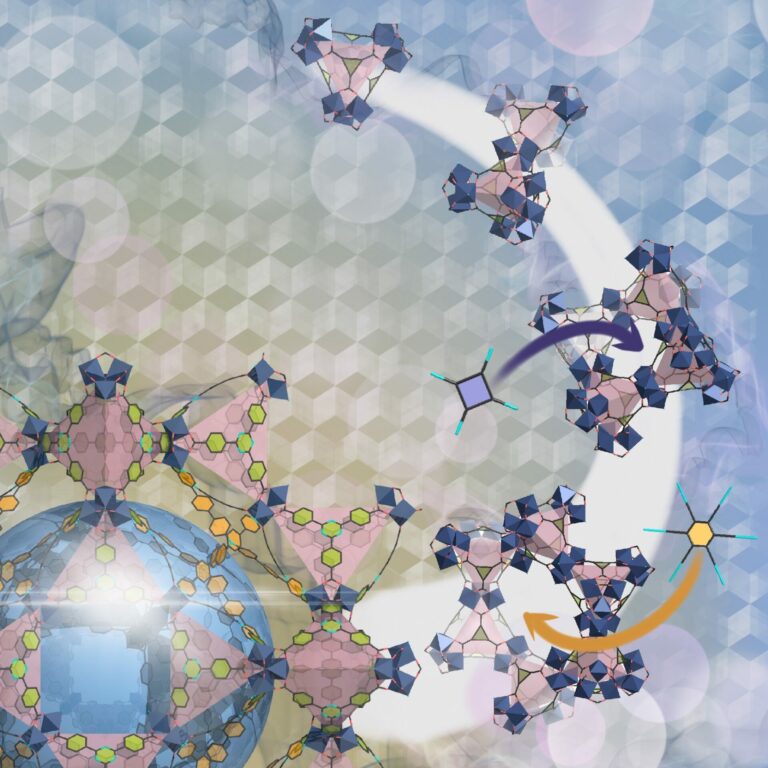
Chemical Engineering
Ancient architecture inspires a window to the future
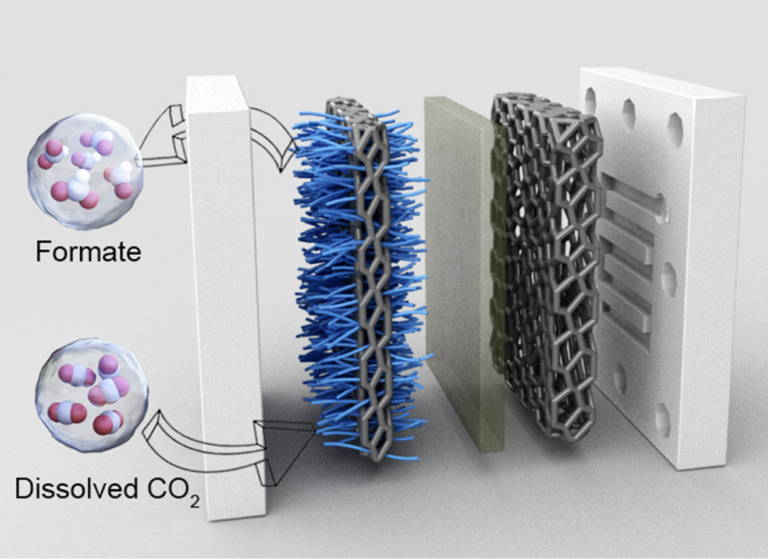
Chemistry
Squeezing more from carbon dioxide
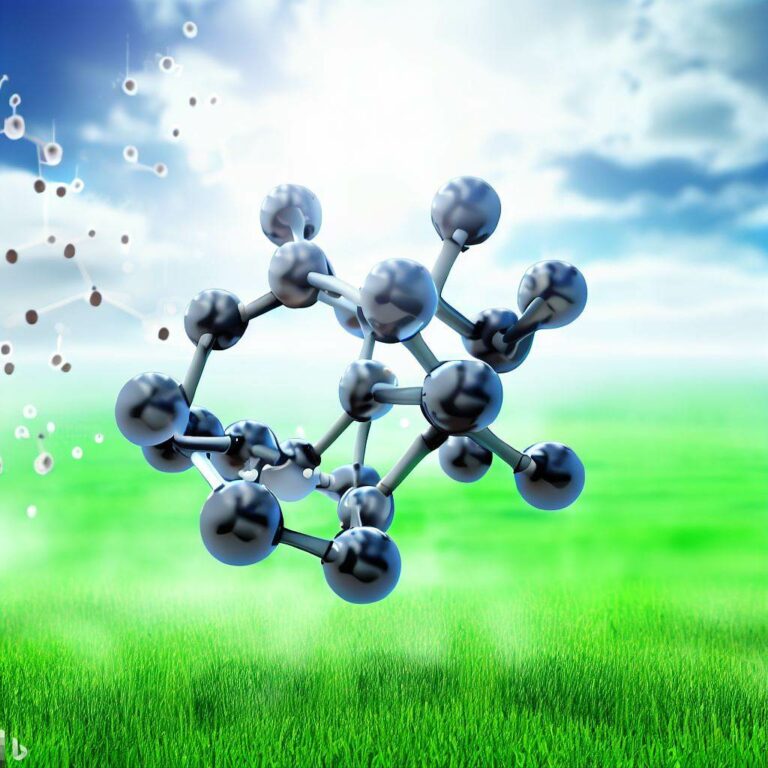
Chemistry
Finding catalytic power in unexpected places
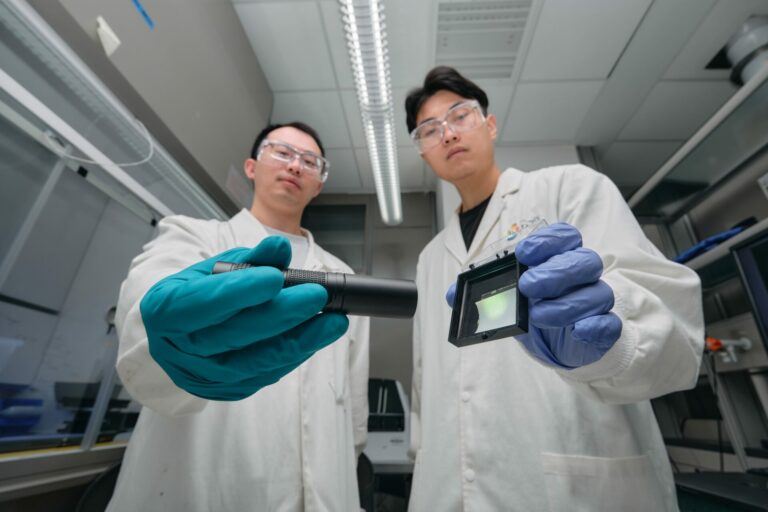
Chemistry
Scintillating new X-ray imaging
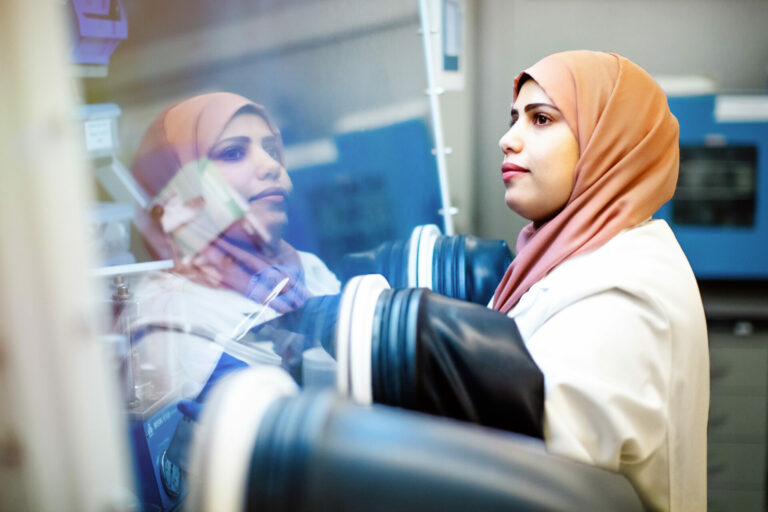
Chemistry