Environmental Science and Engineering
Solar-powered cup brews better brine treatments
Unique membrane design prevents salt crusts from being produced during the distillation of brine water.
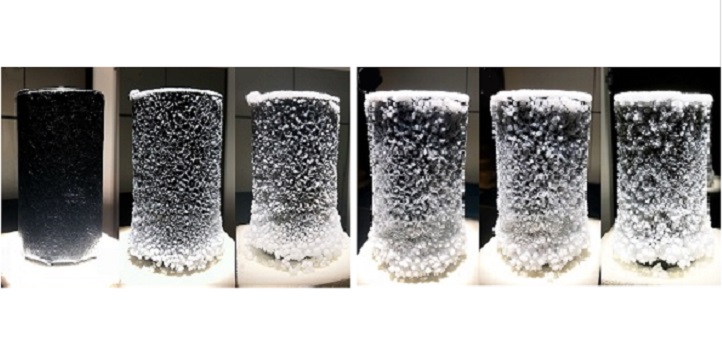
A new distillation device can better recycle contaminants produced by a desalination plant to dramatically reduce waste.
When sea water is purified using reverse osmosis membranes, a liquid brine containing salts and other impurities is often disposed of directly into the environment. Strict regulations are now pushing desalination plants to adopt zero liquid discharge principles to treat this waste water. Current technologies, however, rely on expensive electrical or thermal treatments to concentrate the brine.
A more sustainable approach is now being investigated by Peng Wang and colleagues from the Water Desalination and Reuse Center at KAUST. The team is developing solar photothermal distillation devices that can convert sunlight into heat. When placed upon a typical sample of liquid brine, these photothermal devices can evaporate water with 90 percent energy efficiency.
One problem with using solar distillation devices to isolate clean water from brine is that as liquid evaporates there is a sharp increase in salt concentrations in the effluent. This can cause a thick crust to form on top of the photothermal material, blocking sunlight absorption and reducing the distillation rate dramatically.
Wang and colleagues looked at how salt precipitated on flat, disc-shaped membranes to better understand crust formation. Solar distillation experiments showed that the multilayered silica–carbon–silica structure of their membranes efficiently evaporated pure water, but not brine. After a few hours, salt crystals appeared at the disk edges, eventually spreading to cover most of the membrane, with the exception of the very center.
“When we analyzed these images, we focused on the central areas that are always uncovered even with different salt concentrations,” says Wang. “They helped us realize that structural design may be the key to higher performance, rather than material synthesis.”
Using a simple model, the researchers deduced that the inner diameter of the crust ring could be predicted from the brine’s salt concentration. They hypothesized that by folding the flat membrane into a new shape—a 3D cup with a circular base the exact size of the salt-free zone—they could induce salts to precipitate on the cup’s side above the liquid interface.

The ratio (R/Ro) of the radius of the salt-uncovered area (R) to the radius of the photothermal disk (Ro) relative to brine concentration.
© 2019 KAUST
Tests with the 3D cup produced remarkable results: with optimized height/base ratios, the device recovered nearly 100 percent of brine as solid salt and could run for days without maintenance.
“The insights from this work are quite valuable as we move forward and assess how 3D solar evaporator performs with real desalination brines,” says Wang.
References
- Shi, Y., Zhang, C., Li, R., Zhuo, S., Jin, Y., Shi, L. Hong, S., Chang.j., Ong, C. & Wang, P. Solar evaporator with controlled salt precipitation for zero liquid discharge desalination. Environmental Science & Technology 52, 11822–11830 (2018).| article
You might also like
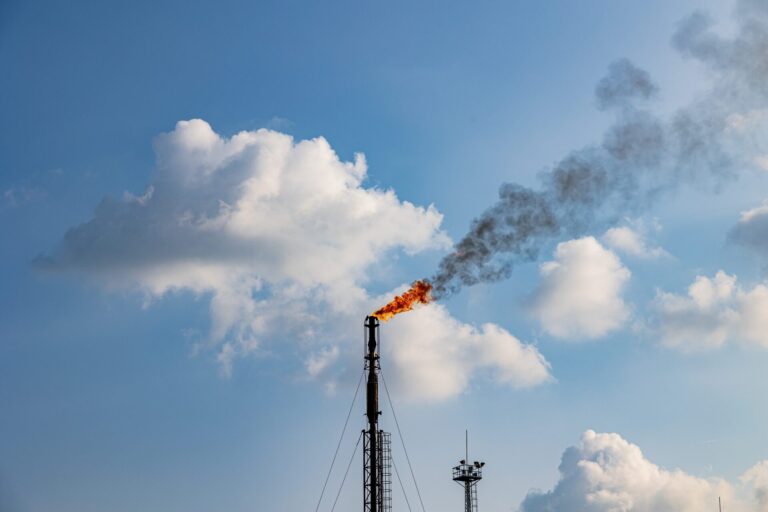
Environmental Science and Engineering
Combat climate change by eliminating easy targets
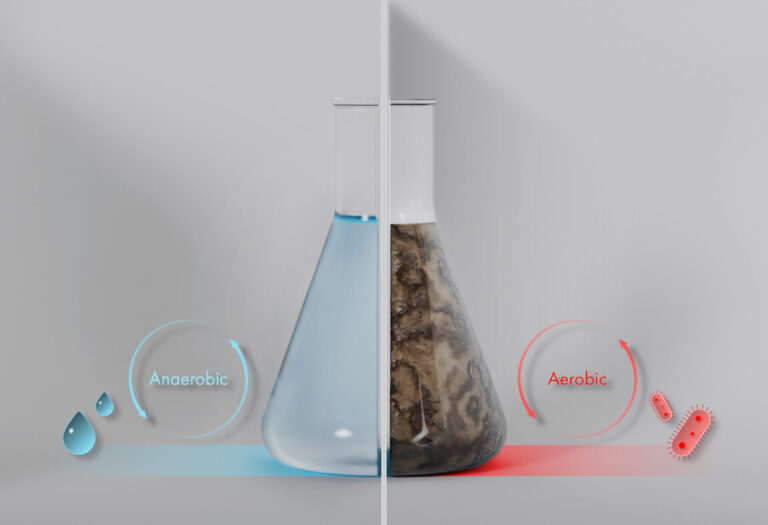
Environmental Science and Engineering
Wastewater treatment to fight the spread of antibiotic resistance
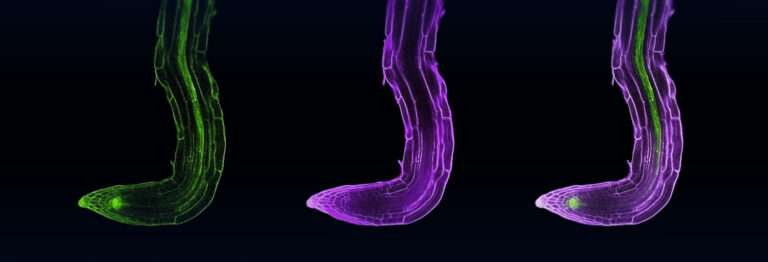
Bioscience
Digging into the world of plant-growth-promoting microbes
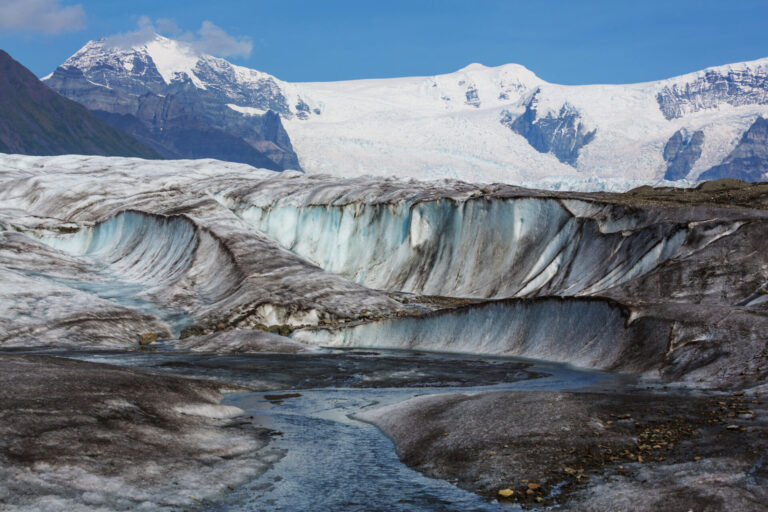
Bioscience
Unique microbiome discovered in mountain streams
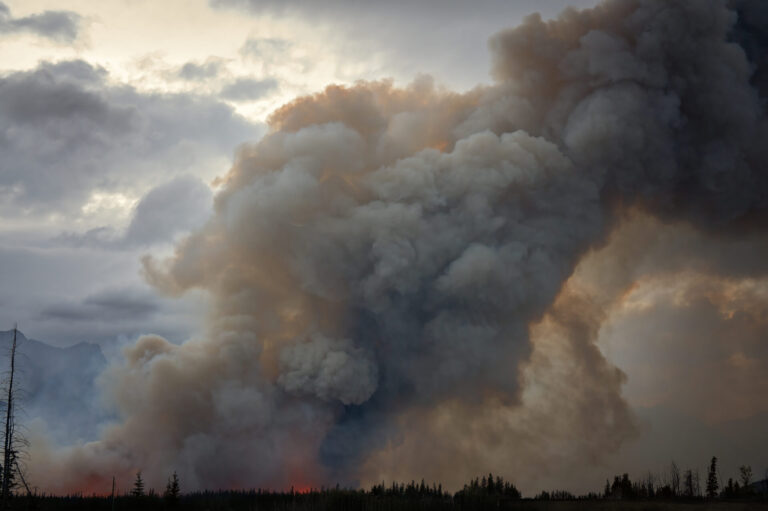
Chemical Engineering
Unveiling the role of biomass-burning aerosols in atmospheric reactions
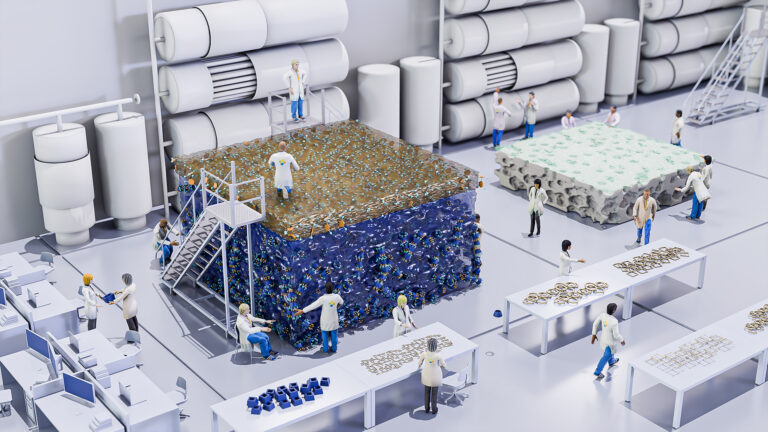
Chemical Engineering
Precision separations with perfect pores
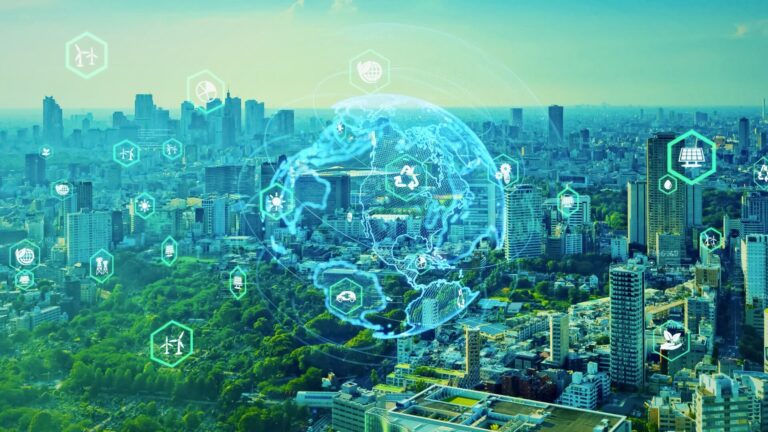
Environmental Science and Engineering
Practical support for building sustainability into our cities
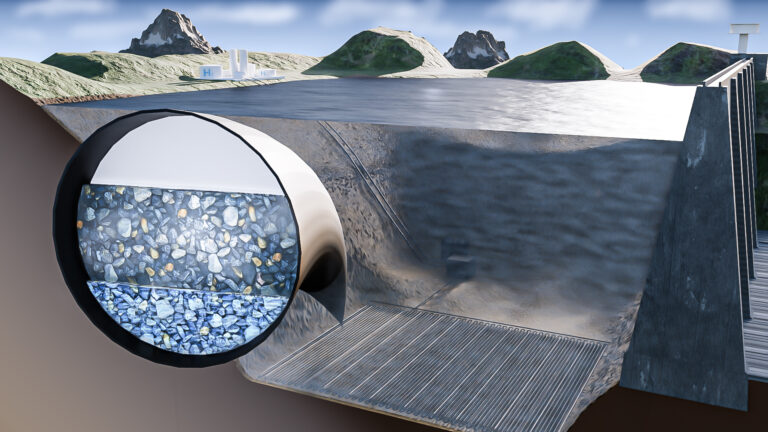
Environmental Science and Engineering