Mechanical Engineering
Sensitive robots feel the strain
Flexible skin for soft robots, embedded with electrical nanowires, combines conductivity with sensitivity within the same material.
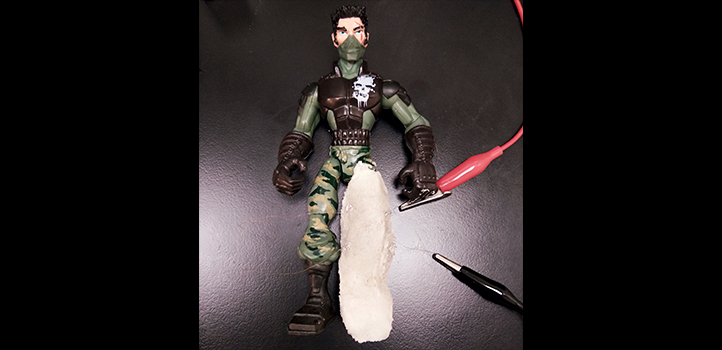
An artificial soft skin imbued with flexible electronics could enhance the way robots sense and interact with their surroundings, KAUST researchers have shown. The team has discovered how to program electrical conductivity and strain sensing into a single material embedded in a stretchy polymer skin. The discovery could also have applications in wearable electronic devices.
When an animal stretches a limb, a network of nerves and sensors within the skin provides feedback that help it orient the limb in space and interact with its surroundings. Embedding a network of strain sensors and connective wiring into a flexible artificial skin would give soft robots similar sensory feedback, helping them autonomously navigate their environment, says Gilles Lubineau, who led the research.
Until now, researchers have used different materials for the sensing and conductive wiring components, adding cost and complexity to the fabrication process, explains Ragesh Chellattoan, a Ph.D. student in Lubineau’s team. “Our objective is to get both sensing and wiring connectivity in the one material,” he says.
The team developed an artificial material comprising a flexible polymer embedded with silver nanowires. Individually, each nanowire is conductive, but high resistance at the junctions between them limits overall conductivity through the material. The resistance increases markedly when the material is flexed and the nanowires are pulled apart such that the nanowire network acts like a strain sensor.
But that behavior can be altered, the team showed. Applying a DC voltage made the nanowire network very hot at the points of high resistance, where the nanowires meet. This localized heating acts to weld neighboring nanowires together, forming a highly conductive, firmly bonded network that is impervious to stretching and flexing. “Electrical welding joins thousands of junctions in the network within 30 seconds,” Chellattoan says. Changing how the current is introduced controls which parts become conductive.
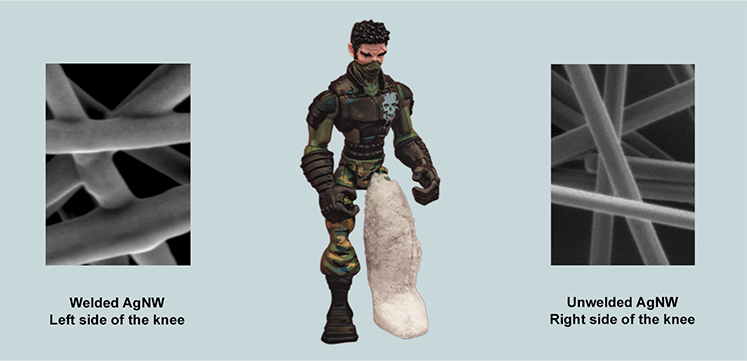
Image shows the difference in the appearance of the nanowire network with and without welding for left and right knees of the action figure, revealing the strong welded joints.
© 2018 KAUST
The researchers created a stretchy skin for a toy action figure to demonstrate their material. They coated one of the figure’s legs with the artificial skin and then applied DC voltage only to the leg’s left side before flexing the leg at the knee and observing what happened. On the right side, the nanowire network acted as a strain sensor that could detect leg position as the figure’s knee was bent and straightened; the left side showed high conductivity regardless of leg position.
The next step, Chellattoan says, is to gain greater control over where nanowire welds form. This would give researchers the ability to draw precise conductive patterns into the artificial skin.
References
-
Chellattoan, R., Lube, V. & Lubineau, G. Toward programmable materials for wearable electronics: Electrical welding turns sensors into conductors. Advanced Electronic Materials 5, 1800273 (2019).| article
You might also like
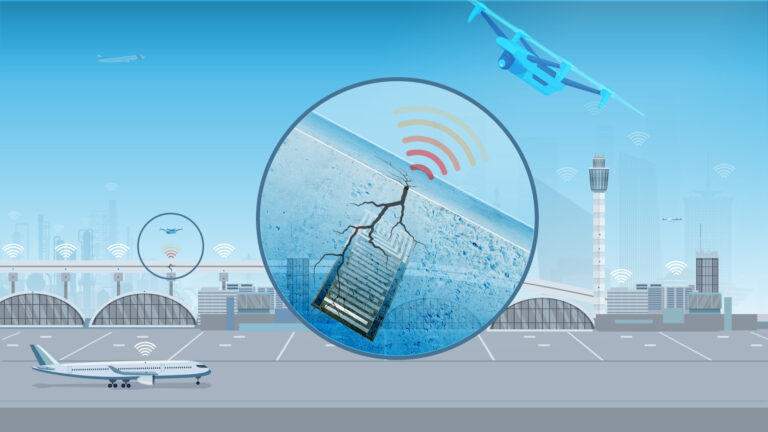
Mechanical Engineering
Innovative strain sensor design enables extreme sensitivity
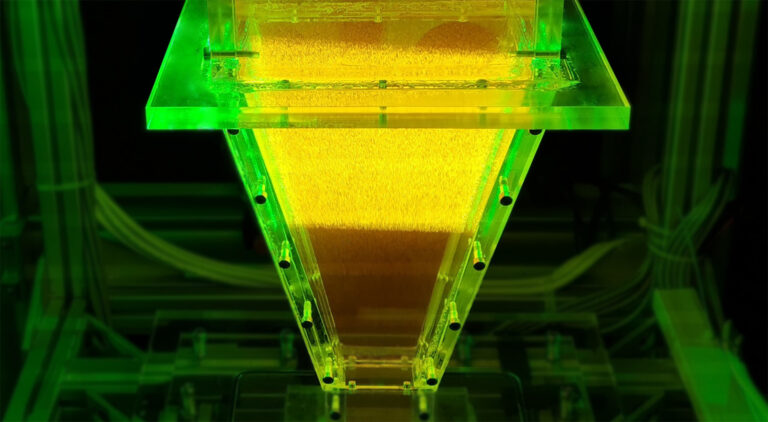
Mechanical Engineering
Turbulent flow shows surprise patterns that could help boost efficiency
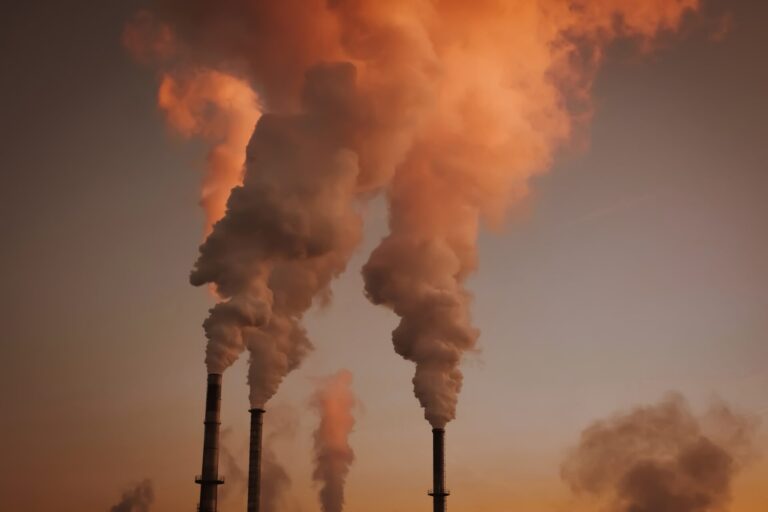
Mechanical Engineering
Machine learning model identifies gas molecules
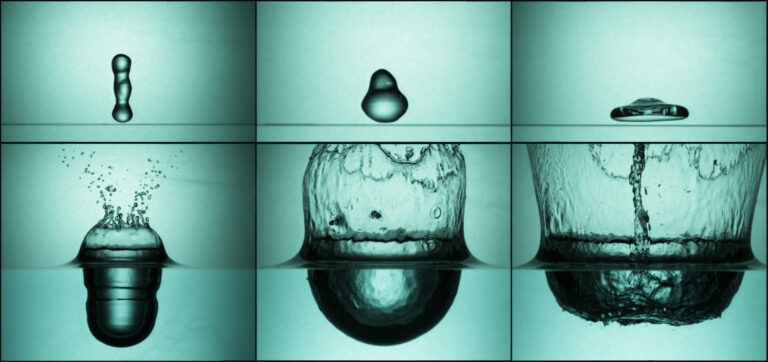
Mechanical Engineering
Making a splash: unraveling the impact of large water droplets
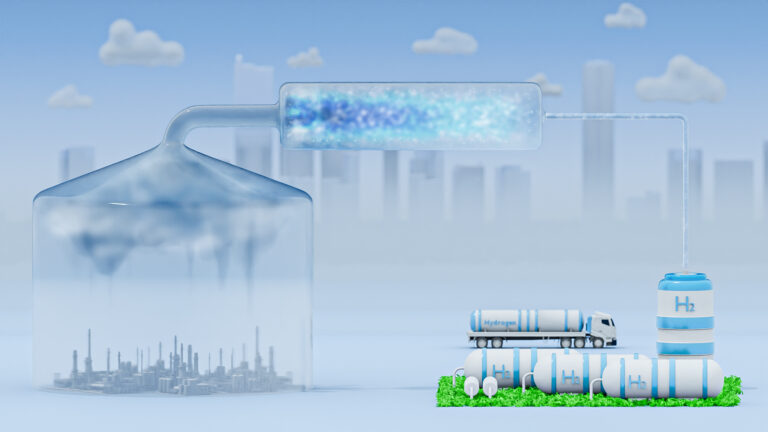
Mechanical Engineering
Sour gas has sweet potential for hydrogen production
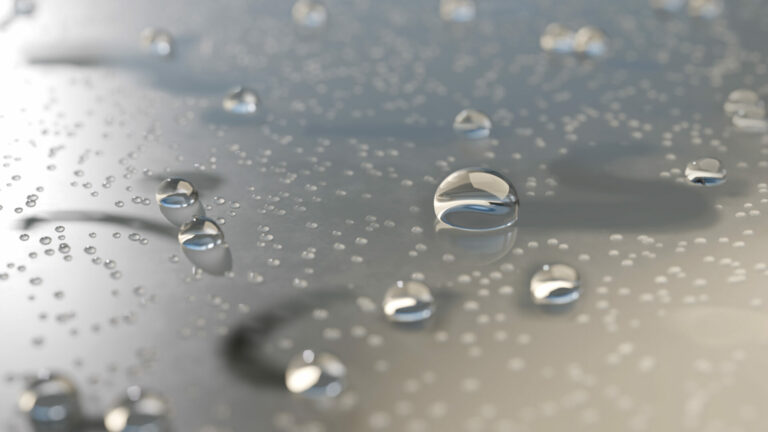
Mechanical Engineering
Dancing droplets’ new spin on water harvesting
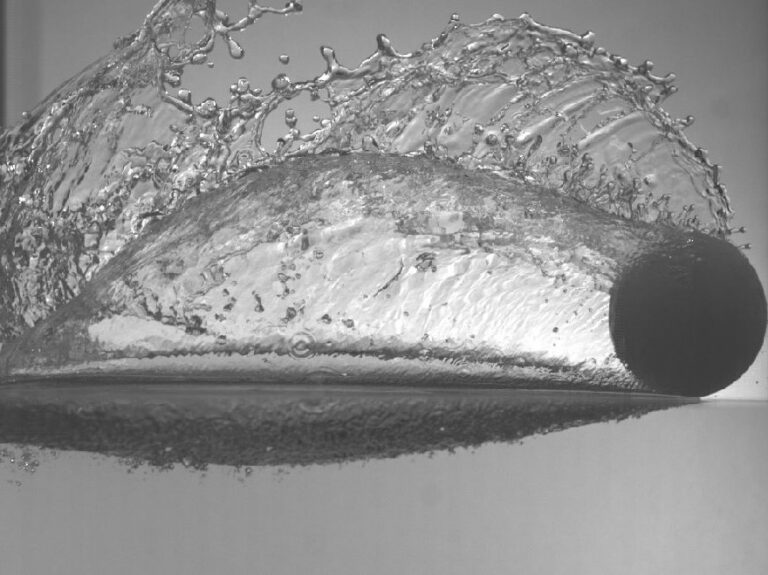
Mechanical Engineering
Underwater air pockets smooth out the bumps
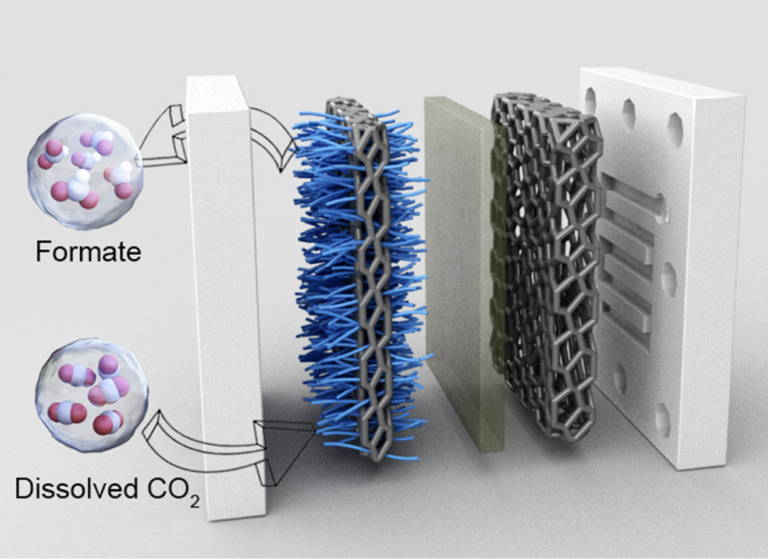
Chemistry