Environmental Science and Engineering
Greening hydrocarbon separation and crude oil refining
Polymer-based membranes that selectively separate hydrocarbon and crude oil mixtures could eclipse current industrial thermal processes.
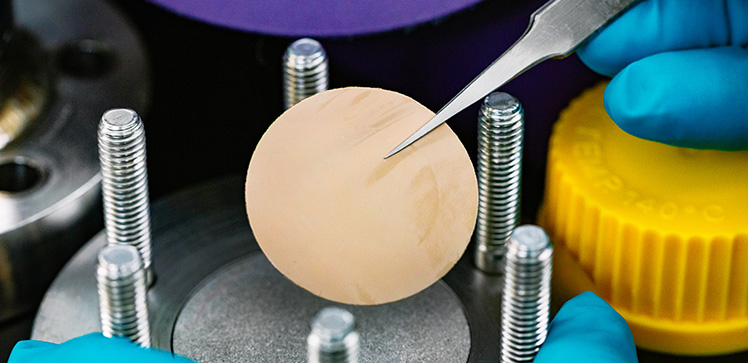
Polymer-based membranes developed at KAUST could enable greener and cheaper industrial separation approaches. Their stability and selectivity can be tuned by thermal crosslinking to separate simple hydrocarbon mixtures and complex crude oil fractions.
Separation processes, such as distillation and evaporation, are central to the chemical, pharmaceutical and petrochemical industries, but they are also energy intensive, expensive and polluting. Each year, crude oil refineries consume about one percent of the total energy used worldwide, and some refineries can even release up to 20 to 35 million tonnes of carbon dioxide (CO2) into the atmosphere.
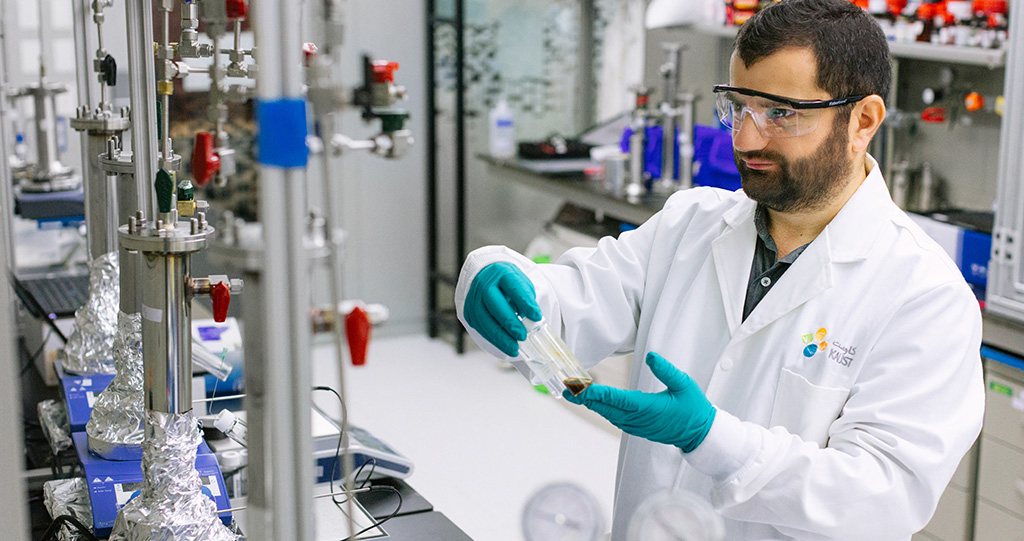
Professor Suzana Nunes and Stefan Chisca (pictured) are planning to scale up the membranes and manufacture test modules for trials in pilot plants.
© 2022 KAUST; Anastasia Serin.
“Decreasing greenhouse gas emissions is a step forward in addressing climate change,” says lead author Stefan Chisca, a research scientist at KAUST. Membranes, with their low carbon footprint and ability to fit in small spaces, offer an attractive alternative to these heat-based processes and can reduce the CO2 emissions of crude oil refineries.
Polymer membranes are cheaper and easier to manufacture and adapt to large-scale processes than inorganic membranes. Yet, their low stability under harsh industrial conditions, such as elevated temperature and certain solvents, affects their performance.
The researchers chose the polymer polytriazole, which bears hydroxyl functional groups as a stable backbone, for their membrane. They deposited the polymer dissolved in various solvents onto a glass plate and immersed the support in distilled water to remove the resulting film. Next, they heated the film in a furnace to crosslink the hydroxyl groups and generate a membrane stable in organic solvents as well as in highly acidic and basic media.
Crosslinking is necessary for challenging applications and must provide stability in the broadest range of conditions, explains team leader Suzana Nunes. “The key to obtaining membranes that could resist harsh environments like crude oil is the presence of the hydroxyl groups,” she says.
The membranes enriched hydrocarbon mixtures by up to 95 percent in compounds containing less than ten carbons. They showed higher selectivity toward paraffins over aromatics, allowing the researchers to target different crude oil mixtures.
“Another crucial factor for the success of these membranes is their asymmetric porous morphology,” Nunes says. The top surface of the membranes presented an ultrathin dense layer consolidated by crosslinking, providing size selectivity. The underlying layers showed a highly porous structure with open interconnected pores that gradually increased with increasing depth to enable permeation.
Chisca explains that the team is now scaling up the membranes and manufacturing test modules for pilot plants. Incorporating a polytriazole membrane unit into existing refineries can improve these processes by producing higher purity components or removing byproducts while reducing energy consumption.
References
- Chisca, S., Musteata, V.-E., Zhang, W., Vasylevskyi, S., Falca, G., Abou-Hamad, E., Emwas, A.-H., Altunkaya, M. & Nunes, S. P. Polytriazole membranes with ultrathin tunable selective layer for crude oil fractionation. Science 376, 1105–1110 (2022).| article
You might also like
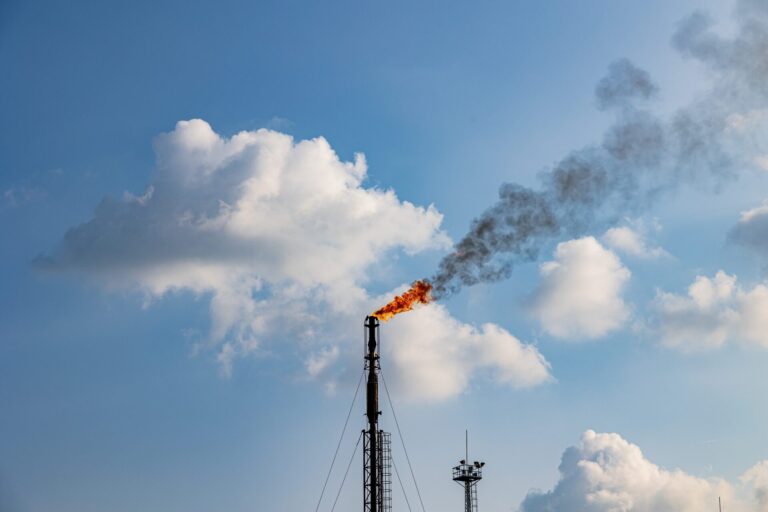
Environmental Science and Engineering
Combat climate change by eliminating easy targets
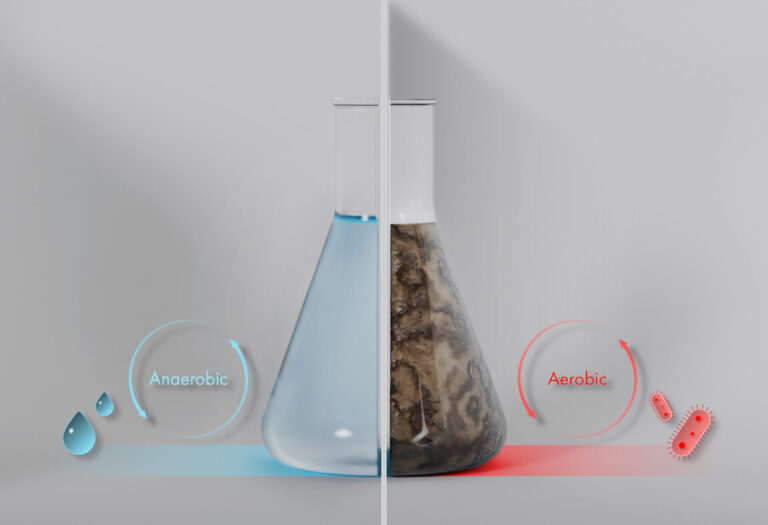
Environmental Science and Engineering
Wastewater treatment to fight the spread of antibiotic resistance
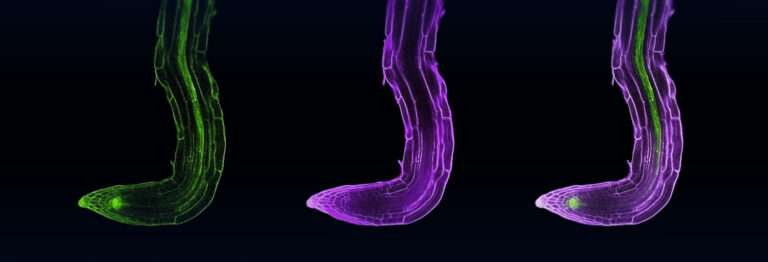
Bioscience
Digging into the world of plant-growth-promoting microbes
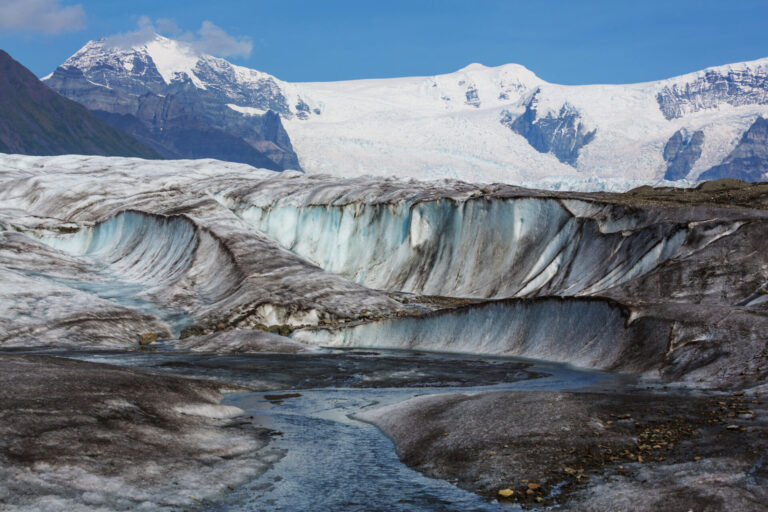
Bioscience
Unique microbiome discovered in mountain streams
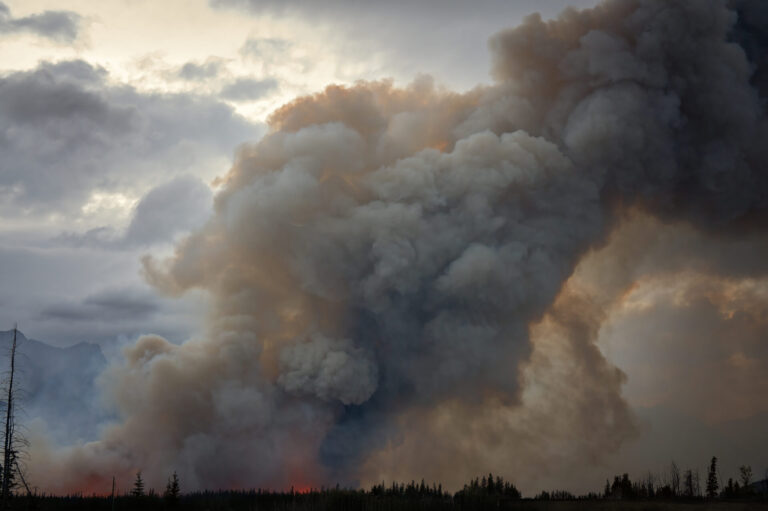
Chemical Engineering
Unveiling the role of biomass-burning aerosols in atmospheric reactions
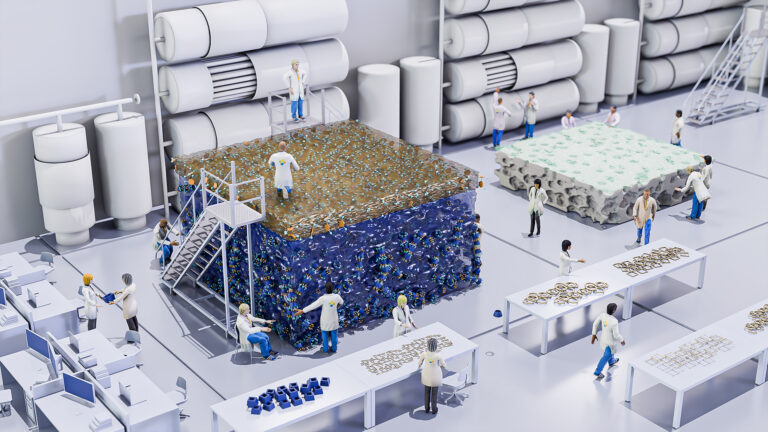
Chemical Engineering
Precision separations with perfect pores
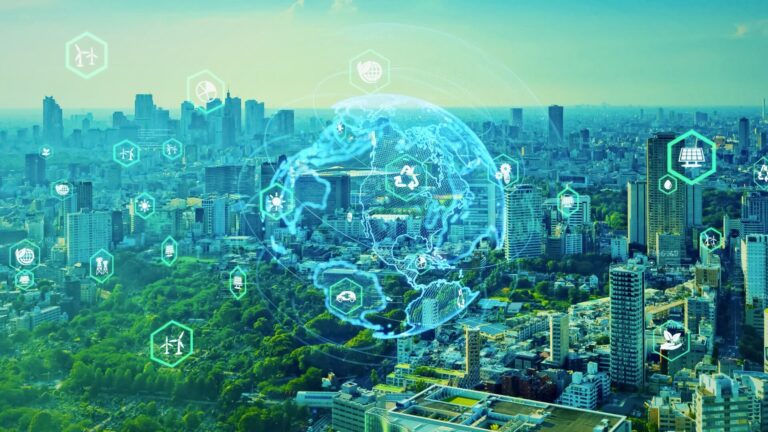
Environmental Science and Engineering
Practical support for building sustainability into our cities
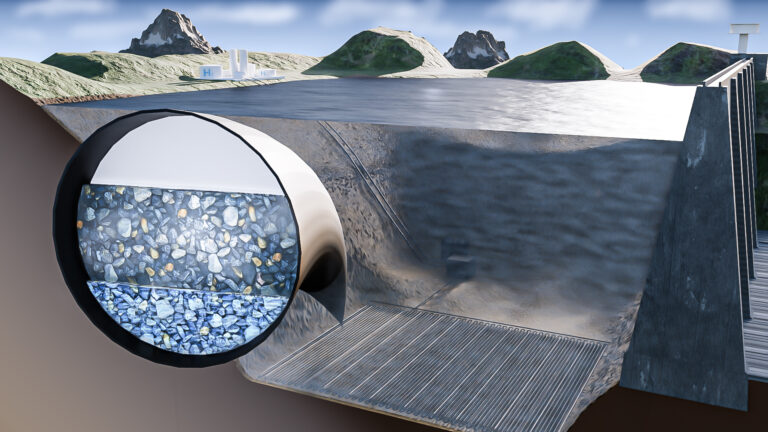
Environmental Science and Engineering