Mechanical Engineering
Vibrating beams feel the pressure
Variations in the vibrations of beams of silicon create a sensitive way of measuring pressure changes.
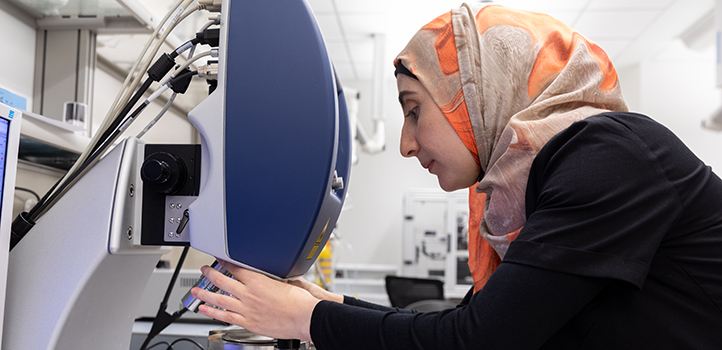
The sensor can be tailored for a specific application by changing the beam’s thickness. 2020 KAUST
A micrometer-scale, low-power consumption pressure sensor has been developed by KAUST scientists, with potential applications in vacuum environments.
Sensors are the interface between automated systems, such as computers and robots, and their environment. Sensors measure light, temperature, motion, mass, pressure, position and much more. The push is to make sensors smaller so that they can be integrated into portable products. Pressure sensors, for example, are used in industrial control, healthcare, medical testing and meteorology. Depending on the application, these sensors need to be sensitive to small changes, quick to respond to these changes, and work over a wide range of pressures.
Nouha Alcheikh, Amal Hajjaj and Mohammad Younis have now developed a sensitive pressure microsensor based on a vibrating beam of silicon just 800-micrometers long, 25-micrometers wide and 1.5-micrometers thick. “We have developed a scalable and sensitive micropressure sensor that operates over an extended range of pressures in the nanoregime,” says Alcheikh.
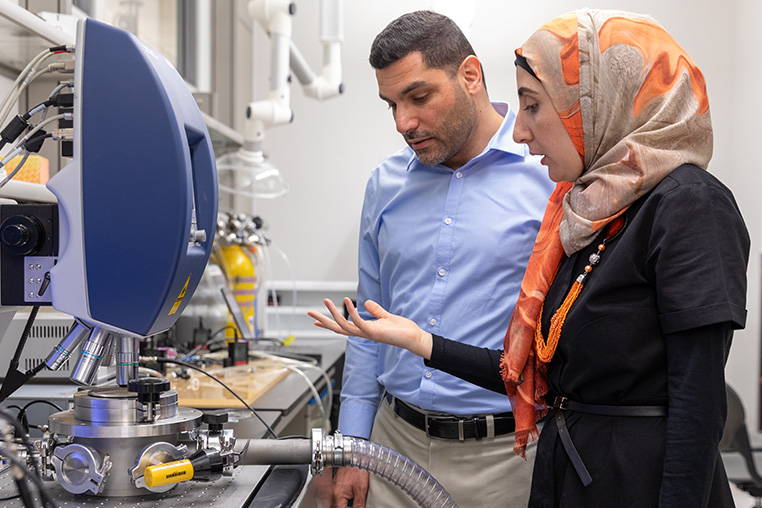
Mohammad Younis (back) and Nouha Alcheikh discuss the optimum thickness for the beam in their pressure sensor.
© 2020 KAUST
A suspended beam will oscillate at a resonant frequency that is determined by its mass, length, density and stiffness. As a current is passed through the beam, it gets hotter and begins to bend. This increased curvature increases the stiffness of the beam and thus moves the resonant frequency. Air surrounding the beam cools it down: the higher the pressure, the more air, the better the cooling. Thus, the resonant frequency of the beam, which can be measured electrically, is related to the pressure.

The pressure sensor the team designed operates over a wide range of pressures with high sensitivity.
© 2020 KAUST
The device the team created operates over a wide range of pressures, from 0.038 Torr to 200 Torr (atmospheric pressure is 760 Torr). The sensor has a sensitivity of 2689 x 10-6 / Torr.
The team also showed that the sensor can be tailored for a specific application by changing the beam’s thickness. They simulated the operation of the beam to demonstrate that the sensitivity becomes higher for a thinner microbeam, but a thicker beam consumes more energy. Thus, an optimum thickness could be calculated for the best sensitivity at low or high pressures, depending on the target environment for the device.
“We are lucky to have the ability to explore wild and new ideas, such as this novel pressure sensor, thanks to the state-of-art facilities at KAUST,” says Younis. “I hope to continue making use of this opportunity to take this device concept into commercialization.”
References
- Alcheikh, N., Hajjaj, A.Z. & Younis, M.I. Highly sensitive and wide-range resonant pressure sensor based on the veering phenomenon. Sensors and Actuators: A. Physical 300, 111652 (2019).| article
You might also like
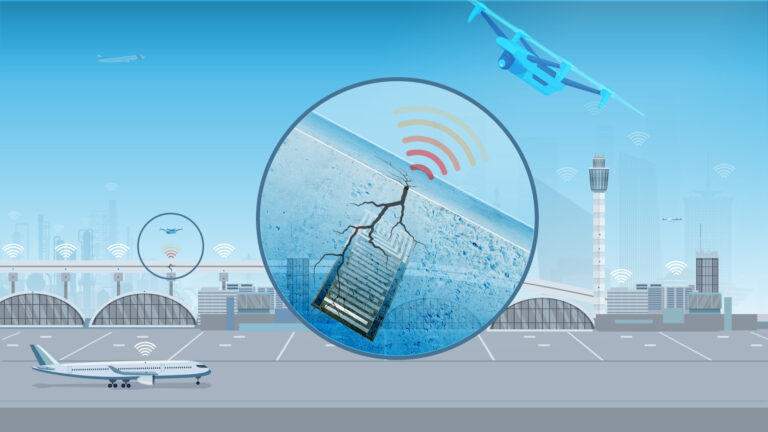
Mechanical Engineering
Innovative strain sensor design enables extreme sensitivity
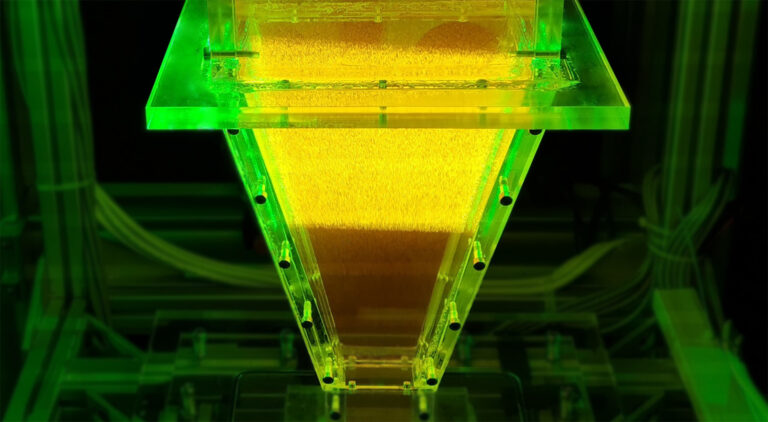
Mechanical Engineering
Turbulent flow shows surprise patterns that could help boost efficiency
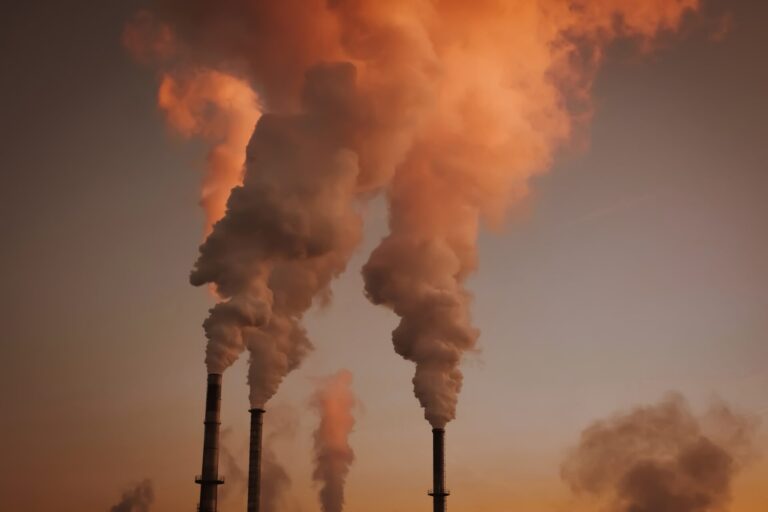
Mechanical Engineering
Machine learning model identifies gas molecules
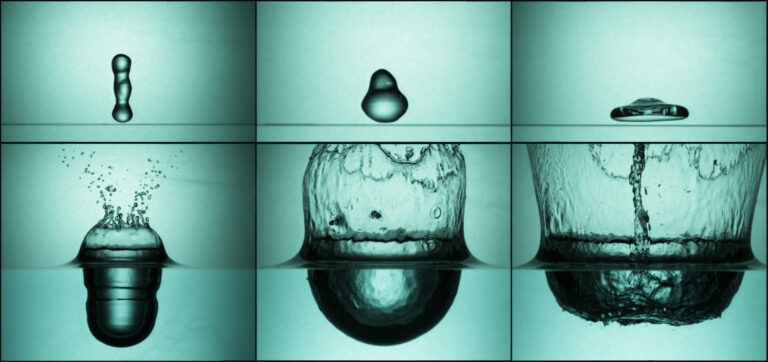
Mechanical Engineering
Making a splash: unraveling the impact of large water droplets
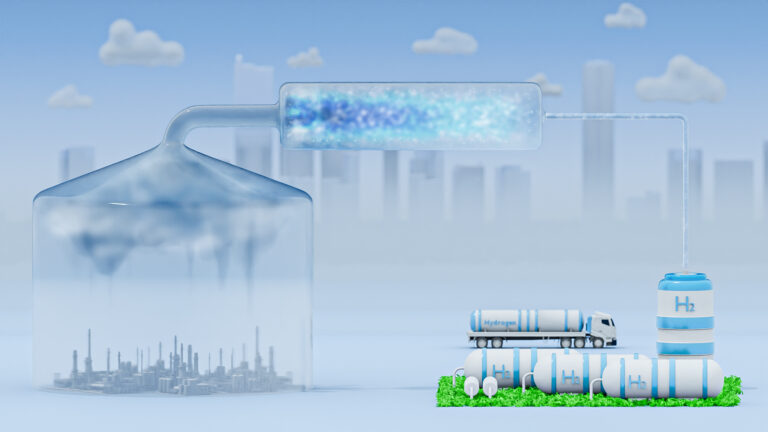
Mechanical Engineering
Sour gas has sweet potential for hydrogen production
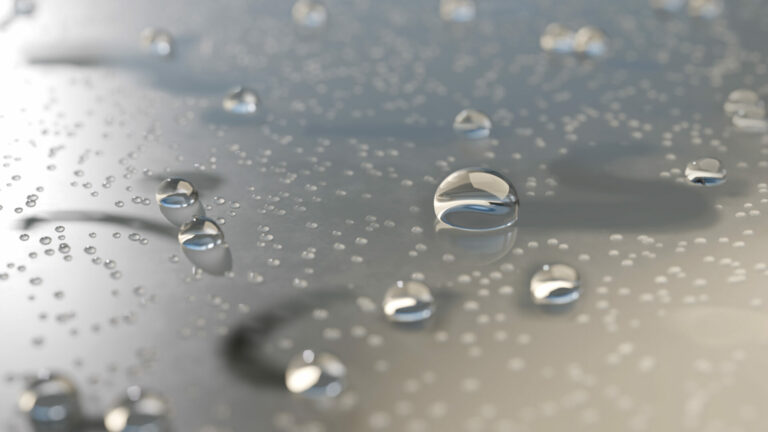
Mechanical Engineering
Dancing droplets’ new spin on water harvesting
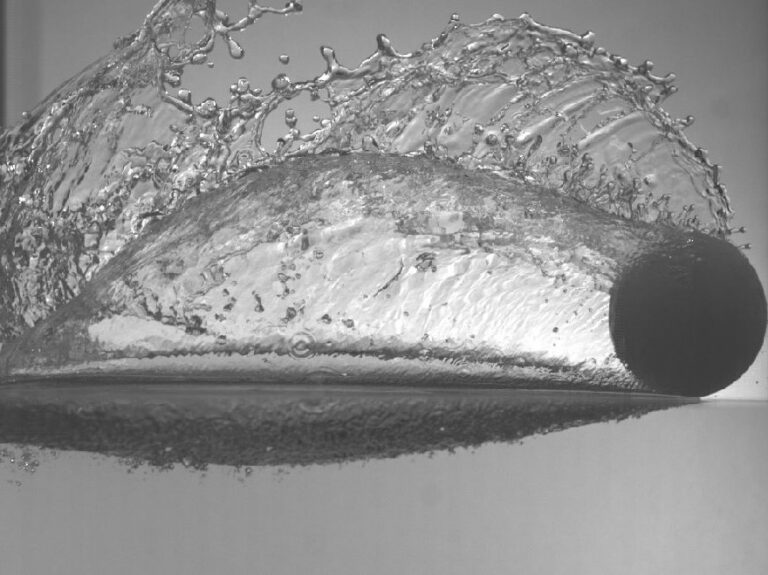
Mechanical Engineering
Underwater air pockets smooth out the bumps
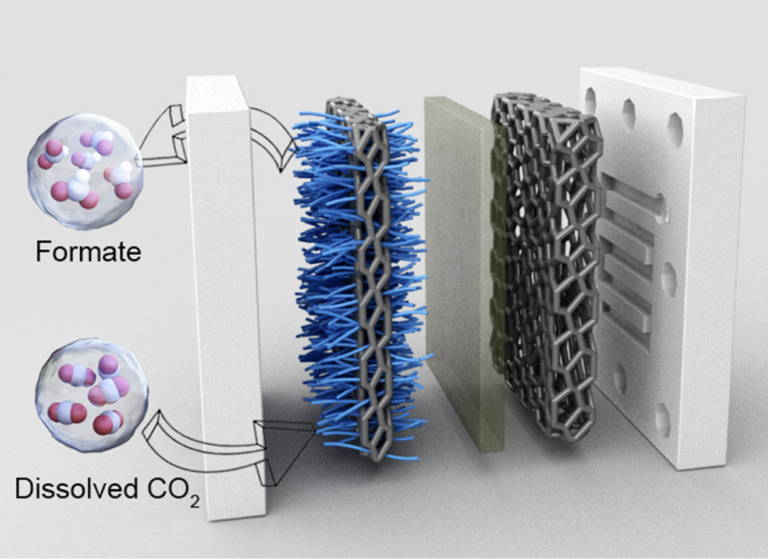
Chemistry