Environmental Science and Engineering
Copolymer membranes toughened up
Innovative chemistry has produced synthetic membranes with improved properties for industry, research and biomedicine.
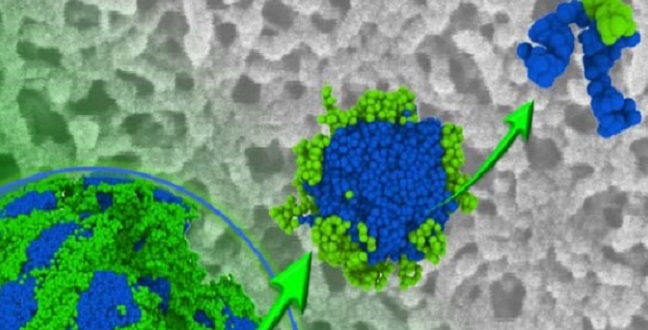
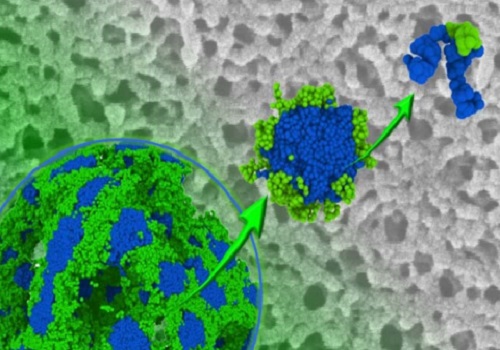
Copolymers (top right) make up porous block copolymer membranes.
Reproduced with permission © 2016 Royal Society of Chemistry
A novel synthetic membrane produced by KAUST researchers is stronger and more stable than previous examples made by the same technique. The new material could fulfill the commercial potential that previous block copolymer membranes have shown.
Porous synthetic membranes are used for filtration in research, industry and biotechnology. They are commonly made from polymers, which are materials constructed from repeating building blocks. Membranes made with block copolymers, which are comprised of two types of building blocks, have more uniform pores than single polymer membranes, so they can filter particles more selectively.
Despite their advantages, block copolymer membranes are still not used commercially because their main component tends to be polystyrene. Using this as a foundation makes the membranes easy to fabricate, but it is not strong enough for many applications.
“Polystyrene is not considered to be a high-performance engineering material,” explained Suzana Nunes from the KAUST Biological and Environmental Science and Engineering Division, who led the research work. “It becomes soft at temperatures just above 100 degrees Celsius and is much less stable than polysulfone, another thermoplastic polymer.”
Membranes made solely from polysulfones are currently the most commonly used in different applications, including seawater desalination, the food industry and artificial kidneys. Nunes and colleagues aimed to exploit the desirable properties of polysulfones—stability and the capacity to withstand high temperatures—to create stronger block copolymer membranes.
“The main difference is that we used polysulfone blocks instead of polystyrene blocks,” noted Nunes. “However, there is no commercially available polysulfone block copolymer that is adequate for this application, so we had to synthesize it.”
The chemical reaction required to create polysulfones differs from that required to produce the other polymer needed for the membrane, so Nunes and her team developed a technique for combining the two reactions. Once the polymers were synthesized, the researchers made membranes with a two-stage process called self-assembly and non-solvent induced phase separation, or SNIPS.
Initially, the two polymers were mixed in solution to induce the formation of ordered structures called micelles. They were then placed in water, where they came together to form the final porous membrane.
Stress tests showed that the new membranes were up to 67-fold stronger than polystyrene block copolymer membranes and could withstand higher temperatures, but they were also more ductile than membranes made from polysulfones alone.
Nunes said that these properties make block copolymer membranes more suitable for commercial application, but she now wants to go further.
“We are interested in membrane development to extend their properties for applications that are not covered by current polymeric membranes,” she said.
References
-
Xie, Y., Moreno, N., Calo, V. M., Cheng, H., Hong, P.-Y. et al. Synthesis of highly porous poly(tert-butyl acrylate-b-polysulfone-b-poly(tert-butyl acrylate) asymmetric membranes. Polymer Chemistry 7, 3076–3089 (2016).| article
You might also like
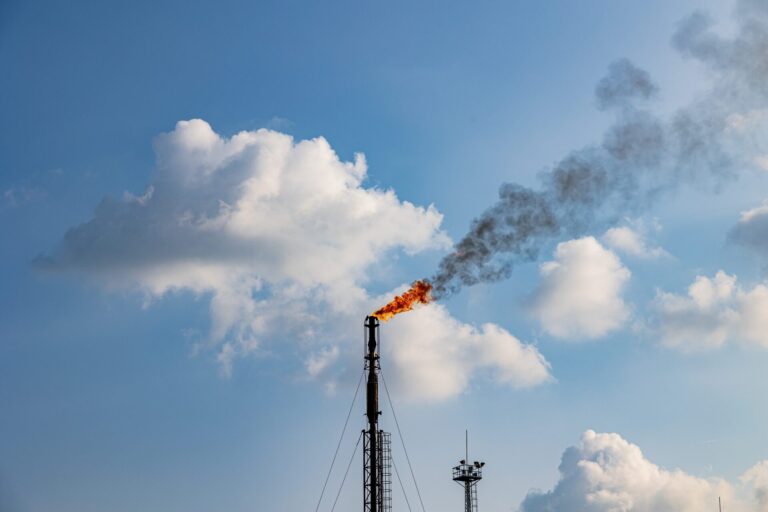
Environmental Science and Engineering
Combat climate change by eliminating easy targets
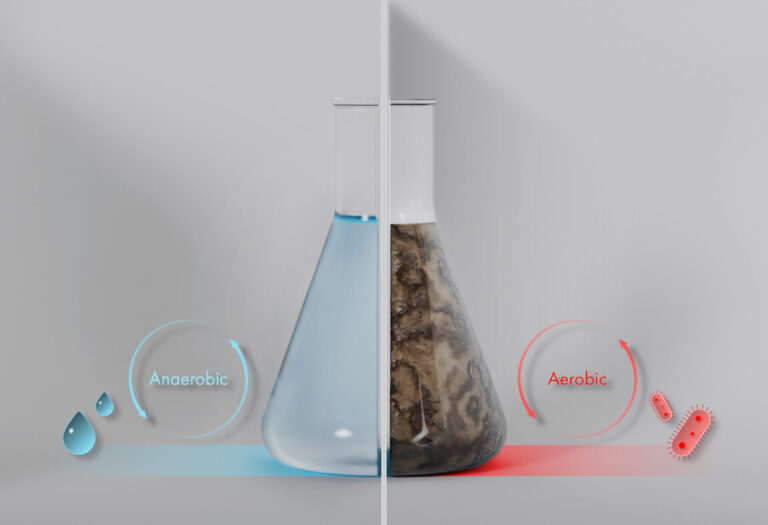
Environmental Science and Engineering
Wastewater treatment to fight the spread of antibiotic resistance
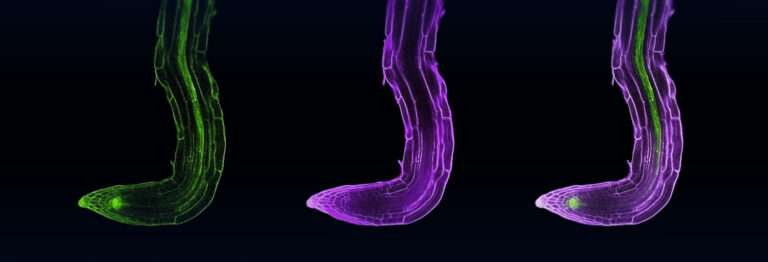
Bioscience
Digging into the world of plant-growth-promoting microbes
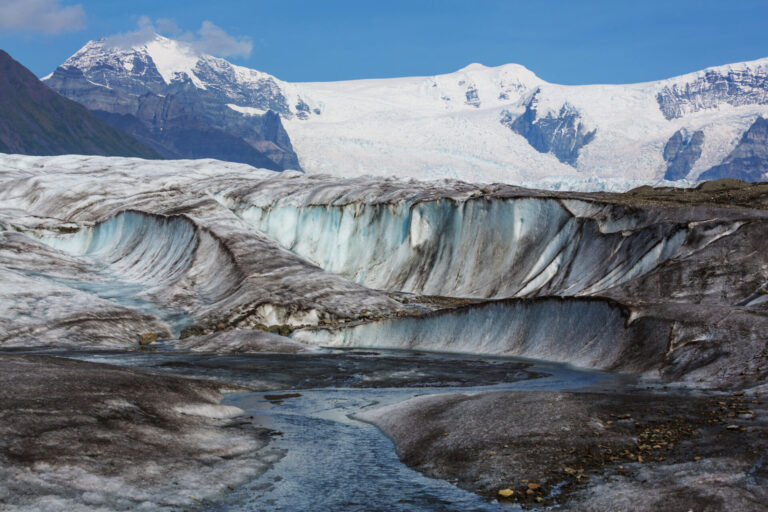
Bioscience
Unique microbiome discovered in mountain streams
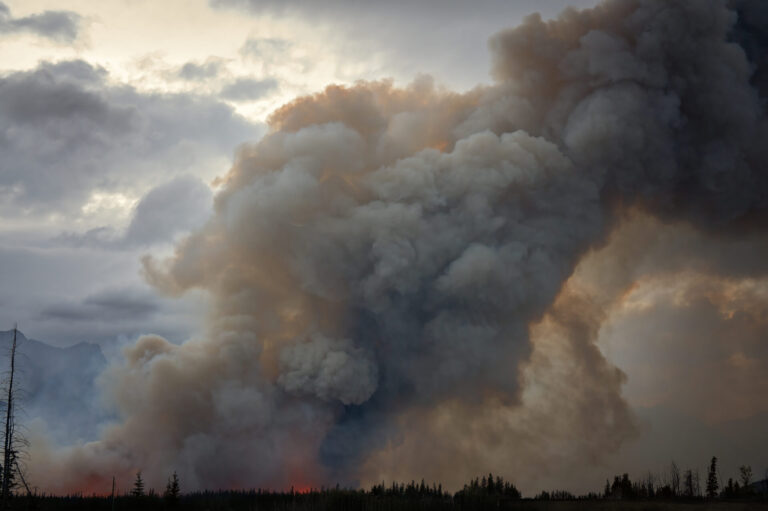
Chemical Engineering
Unveiling the role of biomass-burning aerosols in atmospheric reactions
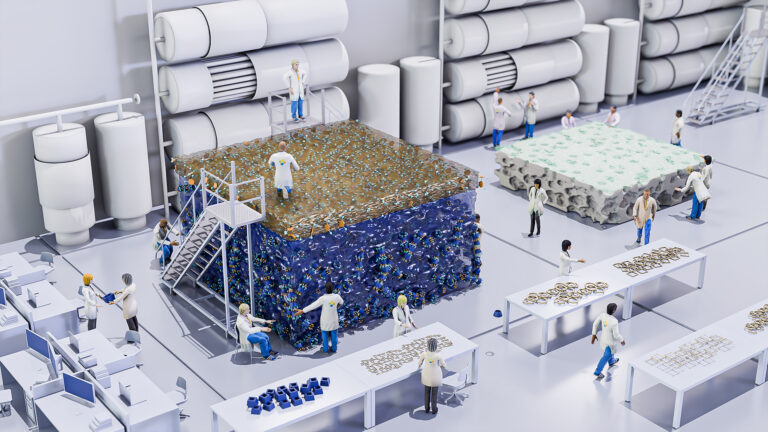
Chemical Engineering
Precision separations with perfect pores
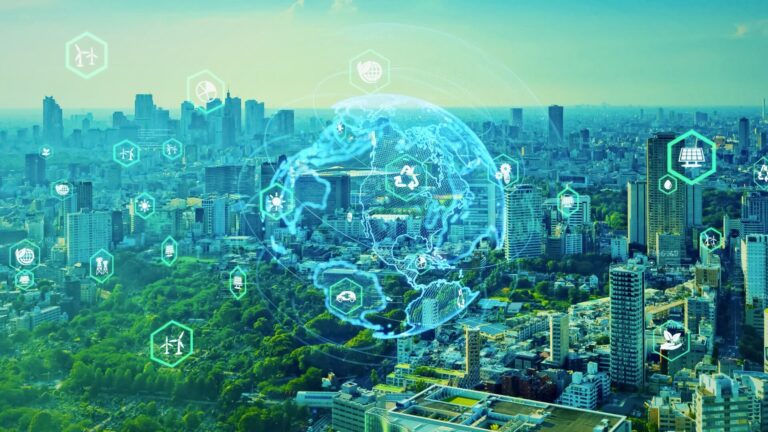
Environmental Science and Engineering
Practical support for building sustainability into our cities
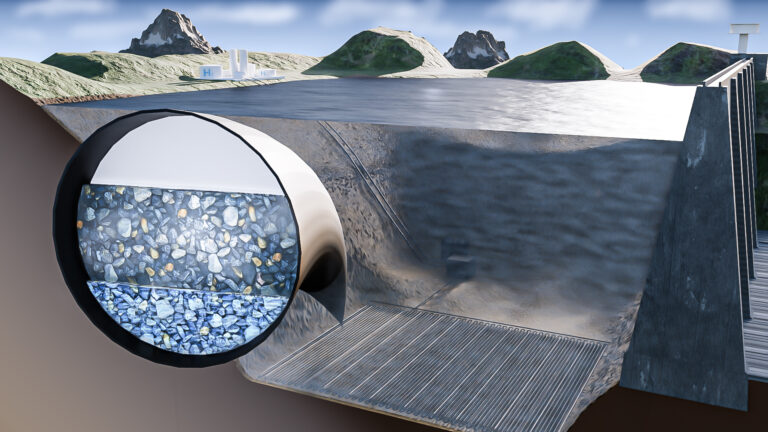
Environmental Science and Engineering