Mechanical Engineering
Tiny drops pack an unexpected punch
Ultrafast cameras spy surprising air-trapping effects intrinsic to droplet-based technologies such as inkjet printing.
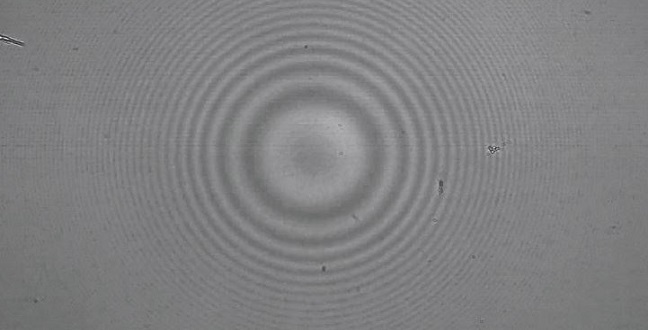
When droplets strike a surface above a moderate speed, their impacts are cushioned by tiny trapped air bubbles. KAUST researchers used cameras capable of snapping 5 million frames per second to show that g-forces and pressure inside such compressible air discs are magnitudes higher than thought possible1.
Inkjet-printed droplets are being used in increasingly diverse fields such as three-dimensional printing, biological assays and semiconductor microfabrication. Because these applications require extremely precise deposition techniques, researchers are scrutinizing the physics of entrapped air layers. Any voids that remain after the droplet solidifies can have an adverse impact on the buildup and appearance of printed materials.
Erqiang Li and Siggi Thoroddsen from KAUST’s High-Speed Fluid Imaging Laboratory noted that the challenge with studying trapped air bubbles is they change shape too rapidly for most methods to resolve. To overcome this hurdle, the team used a state-of-the art video camera that captures images every 200 nanoseconds and a laser-guided technique known as ultra-high-speed interferometry.
The researchers’ approach uses a very precise electronic trigger to start the camera when a water droplet approaches and impacts a glass plate.
Because each frame of the video is illuminated with one of 180 separate laser-diodes, concentric circular patterns known as “fringes”appear when the light reflected from the glass interferes with the light reflected from the drop surface. By examining how the shape and separation of the fringes changed during impact, the scientists captured previously unseen quantitative data on air bubble entrapment.
“The breakthrough advantage of ultra-high-speed-interferometry is that we can follow a particular fringe in time until it contacts the glass, where the fringe separation is zero,” explained Thoroddsen. “This way we can know exactly the distance from the glass – even before the drop touches the solid – with a resolution of 160 nm.”
The high-speed measurements revealed the presence of tiny dimples in droplet bottoms as they crashed into surfaces and trapped air. This was followed by a sudden upward expansion process. The size and potential influence of these bubbles depended on a balance between lubrication pressures that try to help air escape and the incredible deceleration forces needed to cushion the drop’s inertia.
“The bottom of the drop decelerates very suddenly when it is about 10 micro-meters from the surface — we estimate g-forces of 300,000 and the pressure reaches over 10 atmospheres,” said Thoroddsen. “No wonder there’s a proverb that says ‘the drop can hollow the stone.’”
References
- Li, E.Q. & Thoroddsen, S.T. Time-resolved imaging of a compressible air disc under a drop impacting on a solid surface. Journal of Fluid Mechanics 780, 636–648 (2015).| article
You might also like
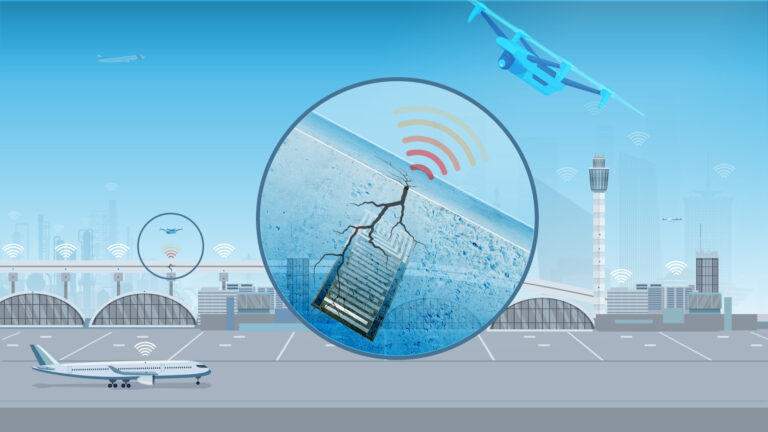
Mechanical Engineering
Innovative strain sensor design enables extreme sensitivity
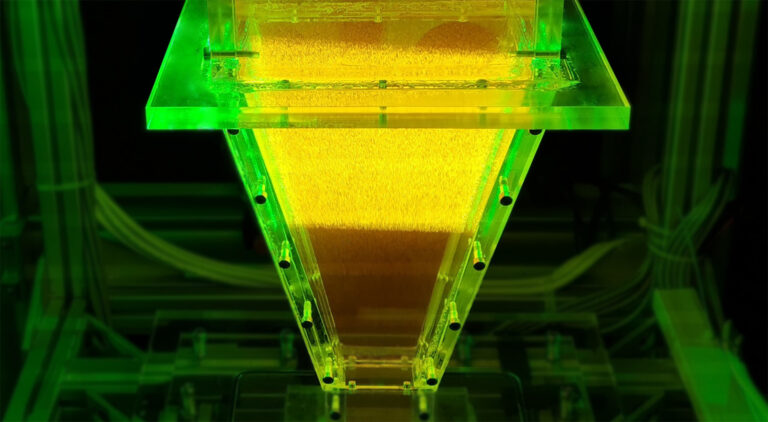
Mechanical Engineering
Turbulent flow shows surprise patterns that could help boost efficiency
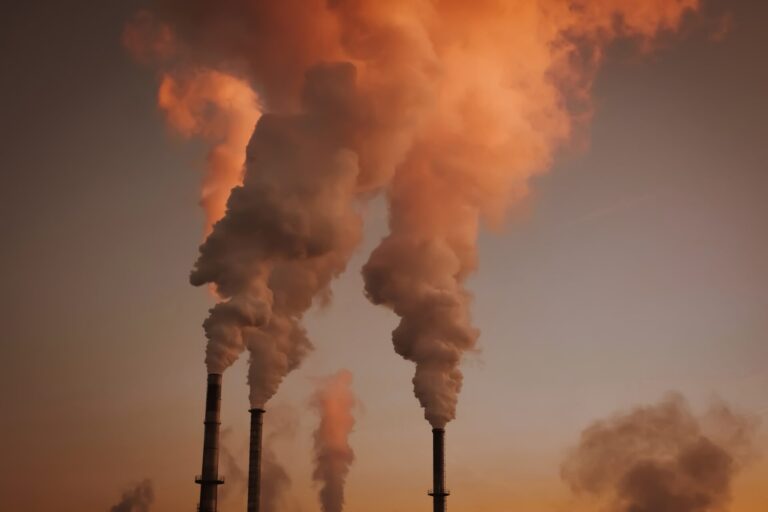
Mechanical Engineering
Machine learning model identifies gas molecules
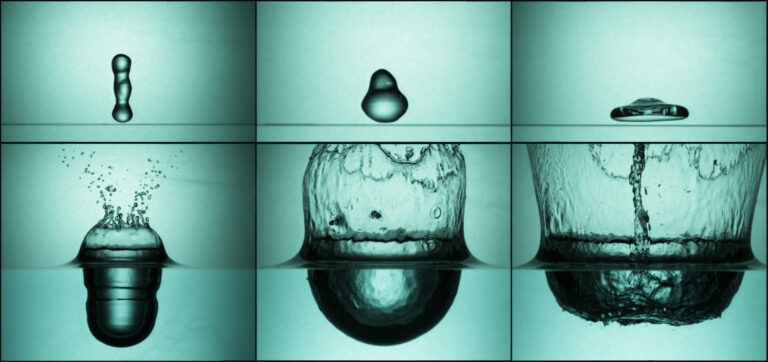
Mechanical Engineering
Making a splash: unraveling the impact of large water droplets
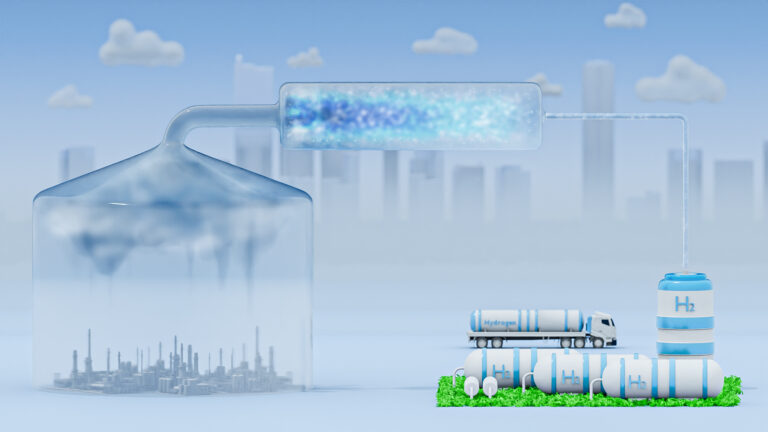
Mechanical Engineering
Sour gas has sweet potential for hydrogen production
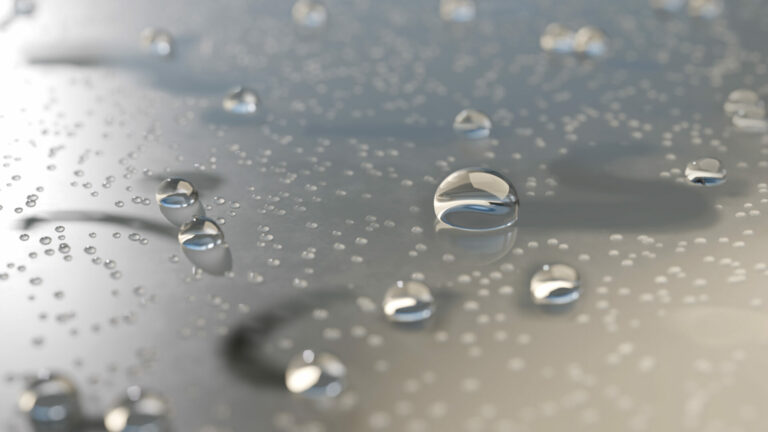
Mechanical Engineering
Dancing droplets’ new spin on water harvesting
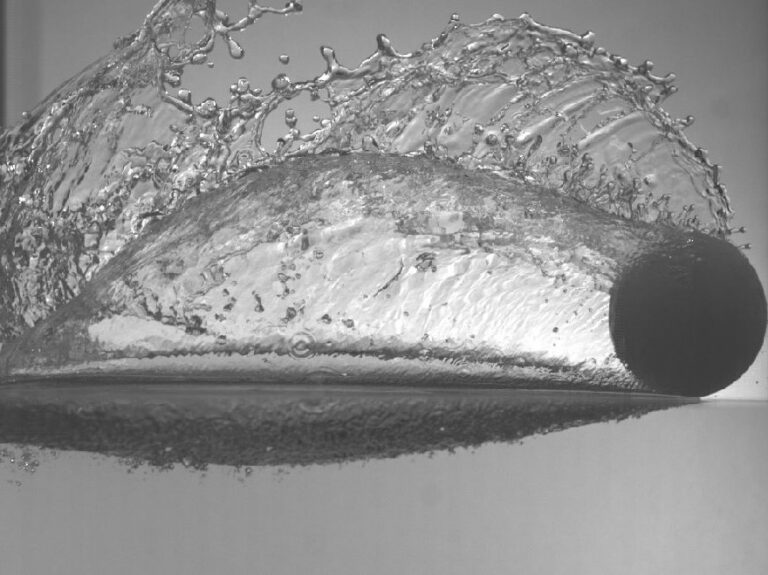
Mechanical Engineering
Underwater air pockets smooth out the bumps
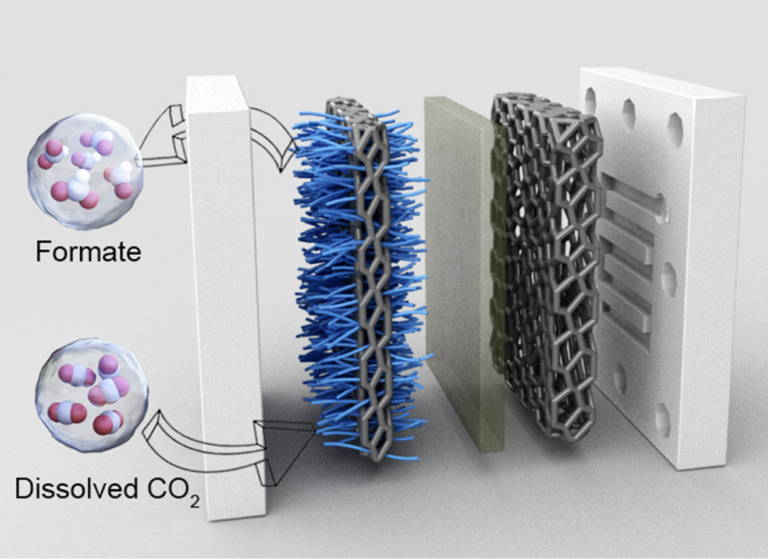
Chemistry