Environmental Science and Engineering
A green separation for industry
Tailor-made membranes offer a cleaner method for the industrial-scale separation of chemical mixtures, says Suzana Nunes. But first we need to make their manufacture greener.
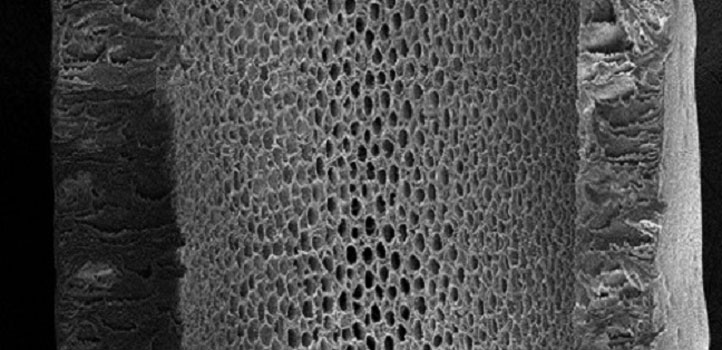
Porous polymeric membranes could really clean up in the chemical and biotech industries, Suzana Nunes believes. Just as permeable membranes have displaced energy-guzzling techniques, such as evaporation for desalinating seawater, membranes could be a far more environmentally friendly option for countless industrial chemical purifications, says the KAUST professor of environmental science and engineering.
Before we make the switch, there’s a challenge to be overcome, Nunes argues. Ironically, despite their environmental applications, the classical process for making the membrane is itself far from green. Most membranes are made using volatile organic solvents, exposing workers to harmful vapors. These solvents are on the EU’s list of the industrial chemicals for which there is the most urgent need to find cleaner, safer alternatives. In many countries, the solvents face a potential ban.
“Industry recognizes the importance of substituting these organic solvents,” Nunes says. “But substitute them with what?”
Taking a lead on green production
That’s where research must come in, Nunes says, and where she herself is taking a lead. Nunes has in mind a two-step solution to the membrane problem: demonstrate to industry a cleaner method for making them; then prove these green membranes perform just as well, or better, than conventionally made membranes for industry separations.
Progress on step one is already well advanced. The classical way to make a membrane is to take a polymer and dissolve it in an organic solvent. The solution is cast in a thin layer, and some of the solvent is allowed to evaporate before it is immersed in water to complete the process, Nunes explains. The size of the pores in the resulting polymer sheet largely decides which components of a chemical mixture can pass through the membrane and which are rejected.
Nunes is championing an alternative approach to membrane fabrication. “Our work has focused on using ionic liquids as a solvent,” she says. Ionic liquids are salts that are liquid at room temperature, but are completely nonvolatile, making them much safer for workers. Ionic liquids have been a hot topic of green chemistry research for the past decade and a wide range is now commercially available.
KAUST professor Suzana Nunes and her team is creating membranes using ionic liquids for more environmentally friendly separations.
© KAUST 2018
Making progress
Nunes and her team at KAUST are already creating membranes using ionic liquids. Many existing high-performance porous membranes incorporate a polymer called polyethersulfone and last year, the researchers showed they could make these using an ionic liquid solvent1. What’s more, the new membrane out-performed a conventionally produced equivalent for separating complex mixtures of peptides and proteins—currently a costly and laborious process for the biotech industry. The applications are vast. For instance, many new medicines are biologic drugs made from proteins, which must be highly purified before being given to patients. The right porous membranes could dramatically simplify this process.
Switching to ionic liquids for membrane making should have other advantages, Nunes argues. “We think we might be able to dissolve polymers that up to now we could not dissolve, and extend the kind of materials we can use for membranes,” Nunes says.
Making membranes from new materials could be of real benefit for many chemical industry separations, where grabbing an existing commercial membrane off the shelf is often not a viable option. The two current biggest uses of membranes—dialysis membranes for healthcare and desalination membranes for fresh water production—involve water-based liquids at benign temperatures. But chemical separations can involve organic solvents, acids or alkalis and high temperatures. These corrosive conditions will rapidly degrade a regular membrane.
In parallel with her work in ionic liquids, Nunes has been developing membranes based on poly(oxindolebiphenylylene), which are impervious to pH extremes and can successfully separate chemical mixtures in organic solvents at unprecedented temperatures of over 300 degrees Celsius2. “This is a topic of real industrial relevance, where we can contribute more and more in the next few years,” she says.
Combining this type of membrane resilience with ionic-liquid-based manufacture is the next challenge researchers must embrace to maximizing membranes’ environmental benefits, Nunes says.
“Ten years from now, I hope we will have convinced the membrane industry, and they will already be using alternative solvents,” she says. “And I’m sure we will be using membranes in the chemical industry much more than they are used now,” she adds. “That’s where researchers like me can contribute most to change.”
References
-
Kim, D.L., Salazara, O.R., & Nunes, S.P. Membrane manufacture for peptide separation. Green Chemistry 18, 5151-5159 (2016).| article
- Pulido, B.A., Waldron, C., Zolotukhin, M.G., & Nunes, S.P. Porous polymeric membranes with thermal and solvent resistance. Journal of Membrane Science 539, 187-196 (2017).| article
You might also like
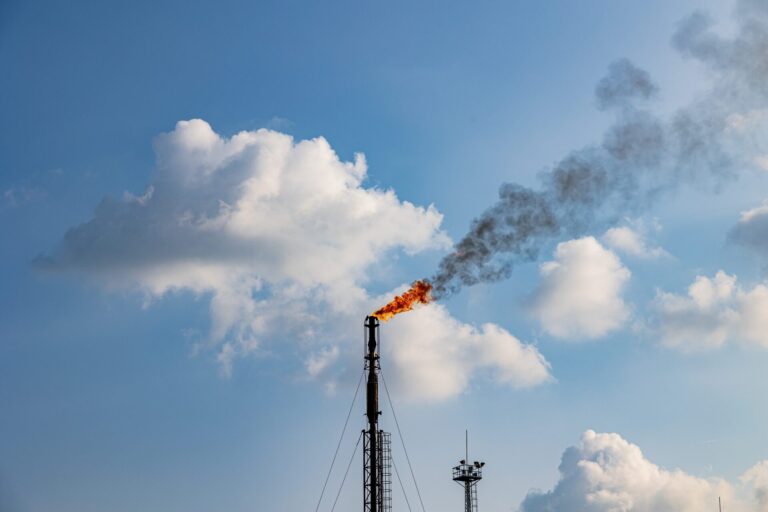
Environmental Science and Engineering
Combat climate change by eliminating easy targets
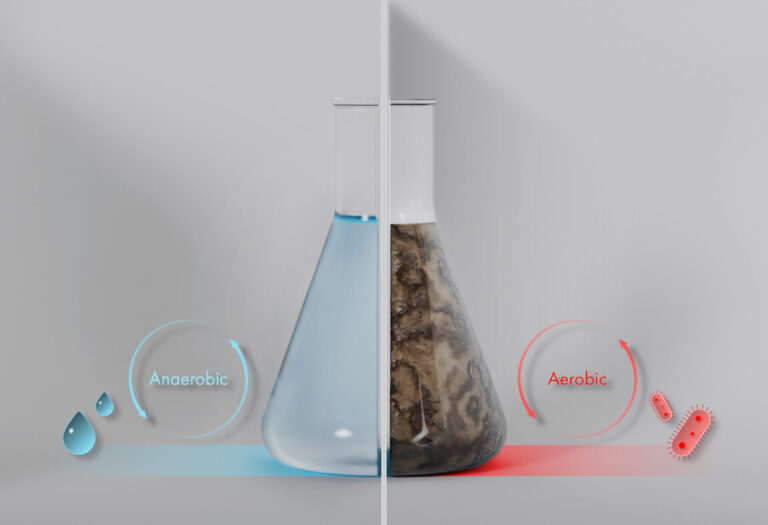
Environmental Science and Engineering
Wastewater treatment to fight the spread of antibiotic resistance
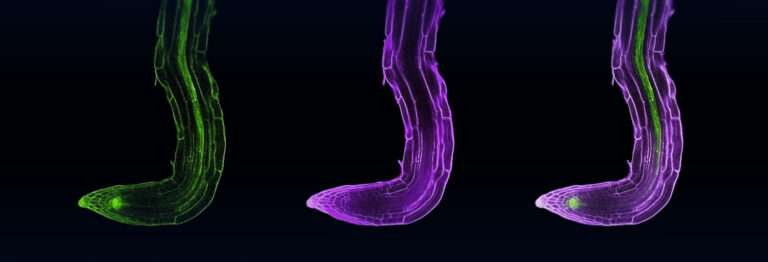
Bioscience
Digging into the world of plant-growth-promoting microbes
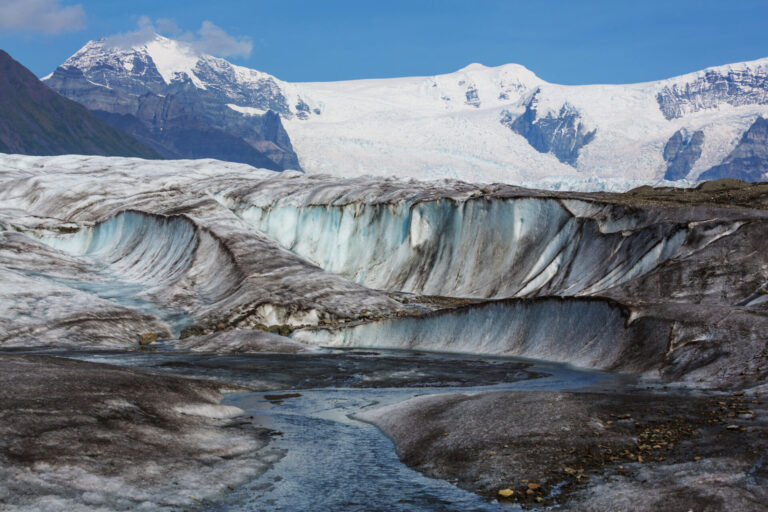
Bioscience
Unique microbiome discovered in mountain streams
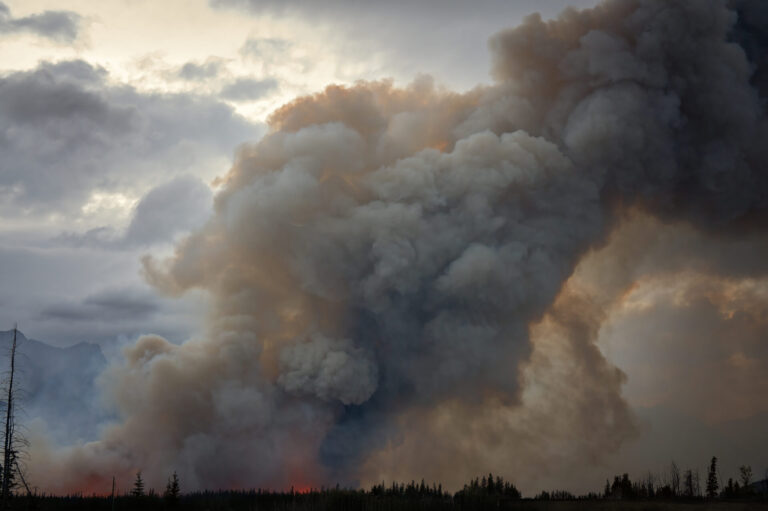
Chemical Engineering
Unveiling the role of biomass-burning aerosols in atmospheric reactions
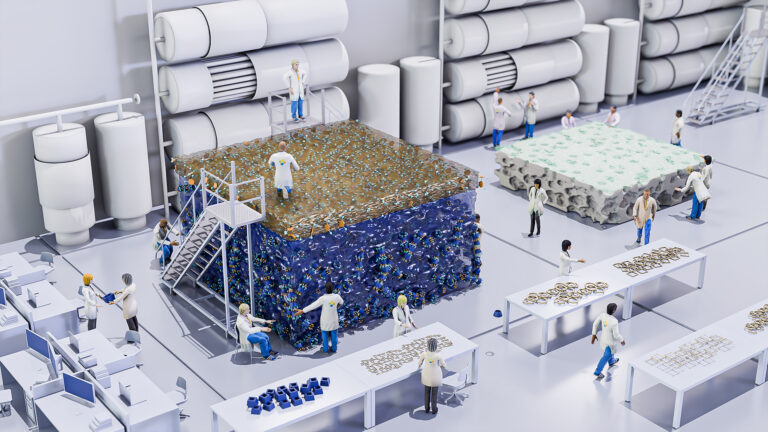
Chemical Engineering
Precision separations with perfect pores
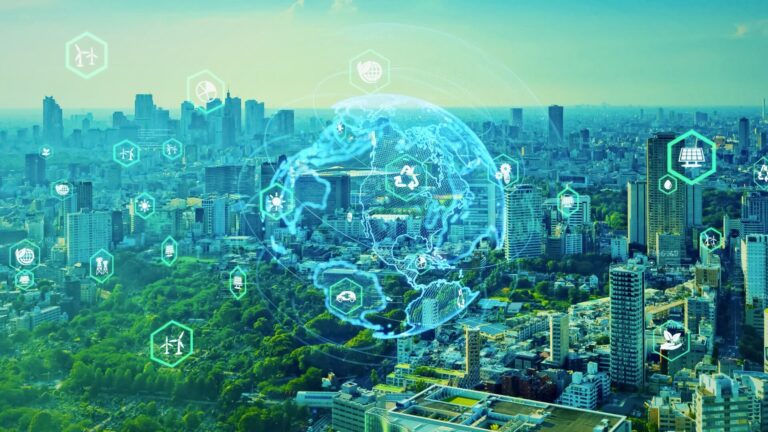
Environmental Science and Engineering
Practical support for building sustainability into our cities
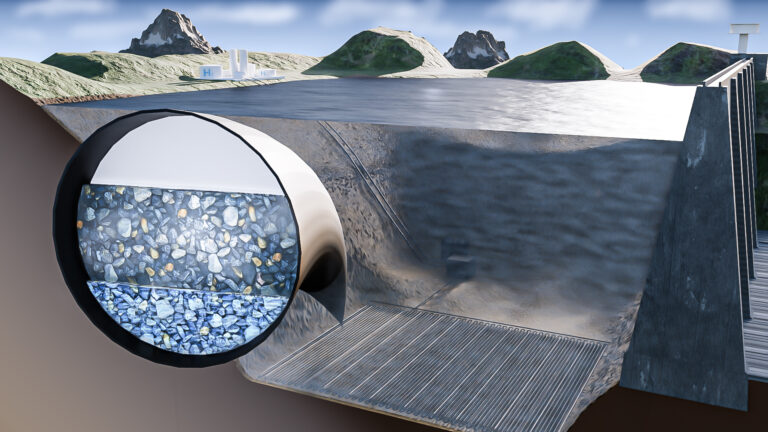
Environmental Science and Engineering