Chemical Engineering
Catalyst generates hydrogen from toxic waste
Understanding hydrogen sulfide decomposition provides a design strategy to improve catalyst activity.
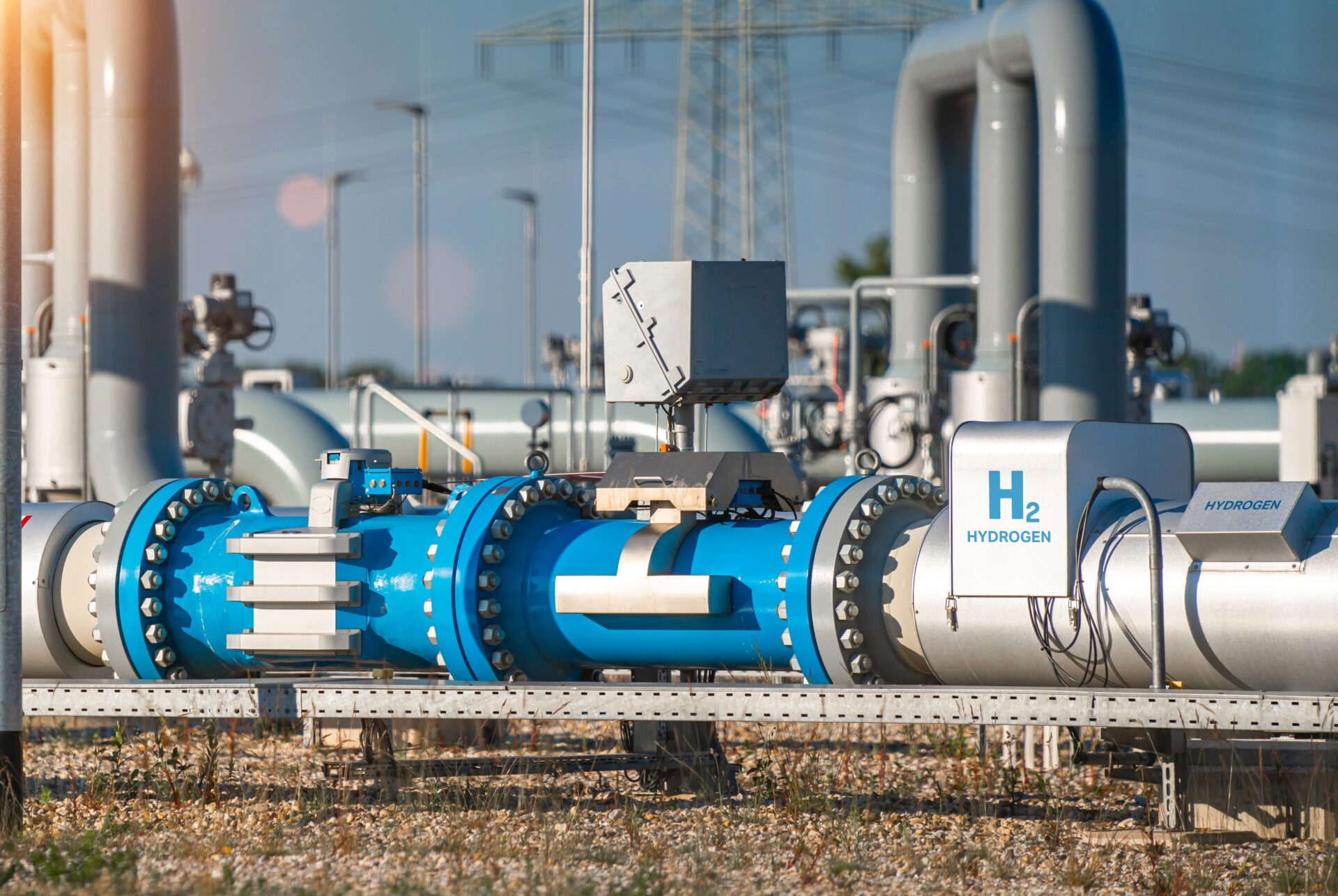
Hydrogen sulfide is a toxic component found in certain types of natural gas and can be generated during refining processes. Now, KAUST researchers have developed a technology that transforms this waste product into sulfur and hydrogen, both useful industrial chemicals[1]. By pinpointing exactly how this reaction works, the research paves the way for further improvements in the catalyst’s performance.
“We have developed a method to engineer a catalyst that has reached very high levels of activity in laboratory conditions,” says KAUST’s Pedro Castaño, who co-led the work in collaboration with the petroleum and natural gas company Saudi Aramco. “A significant aspect of this project is that it is a true partnership, with a very effective exchange of people, ideas and responsibilities,” Castaño says.
Much of Saudi Arabia’s natural gas reserves contain hydrogen sulfide. Aside from its toxicity, hydrogen sulfide also contributes to atmospheric pollution and acid rain, so it must be removed from this “sour” natural gas. The existing industrial Claus process then converts hydrogen sulfide into water and sulfur, which is used in fertilizers and other products.
Some catalysts can turn hydrogen sulfide into sulfur and hydrogen, a clean-burning fuel that could reduce the greenhouse-gas emissions of transportation and industrial processes. In principle, this could increase the economic value of hydrogen sulfide, but to date none of the catalysts have been effective enough to deploy at industrial scale. So the KAUST team studied one of the most promising catalysts, molybdenum disulfide (MoS2), to find ways to improve it.
The atoms in MoS2 are ordered into flat sheets that can adopt two different arrangements called phases. Incoming hydrogen sulfide molecules may bind at several different locations on the faces and edges of these sheets. At some of these sites, the molecules break apart so that their atoms can recombine into hydrogen and sulfur. The efficiency of this process depends on factors such as how strongly hydrogen sulfide binds to the catalyst, and how easily sulfur and hydrogen escape once they have formed.
The researchers’ computer simulations of the two phases showed that the ideal sites were found along the edges of the MoS2 sheets: sites that contain more prominent sulfur atoms being particularly important. “We need a particular balance of edges and imperfections on the MoS2, and when we understand this balance we can engineer the catalyst accordingly,” says Castaño.
The researchers then made three different MoS2 catalysts in the lab so they could study their surfaces and test their activity. They found that a catalyst prepared with a small amount of oxalic acid was the best performer, because the additive helped to generate more of the desirable edge sites.
The experiments also revealed that the strength of hydrogen-atom binding to the catalyst plays a key role in dictating the overall rate of the reaction. By applying the same theoretical approach to other materials, the team discovered that vanadium disulfide and niobium disulfide might also be promising catalysts for this reaction.
All these findings should help to further optimize such technology, so that they can be used for hydrogen sulfide decomposition at an industrial scale.
Reference
- Almofleh, A., Alaithan, Z., Velisoju, V.K., Mohamed, H.O., Mukhambetov, I., Lezcano, G., Castaño, P. & Aljama, H. Designing sulfide catalysts for H2S dissociation to H2 based on reaction descriptors and microkinetics. Applied Catalysis B: Environment and Energy 361, 124605 (2025).| article
You might also like
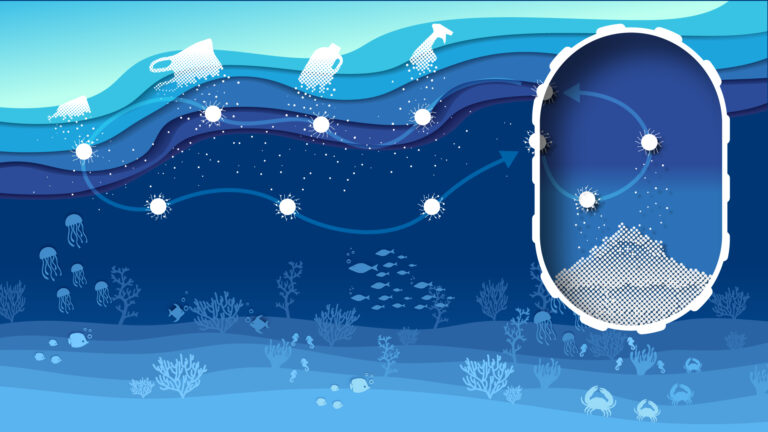
Chemical Engineering
Magnetic nanoparticles capture microplastics from water
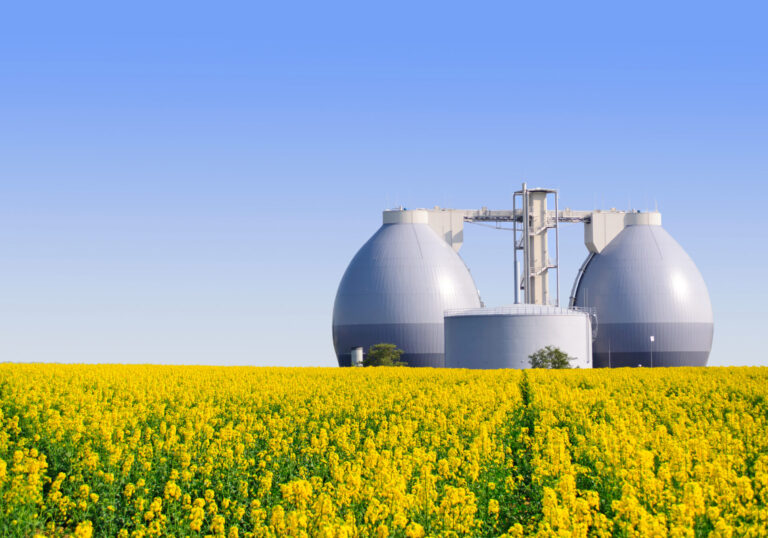
Chemical Engineering
Biogas upgrading goes with a swing
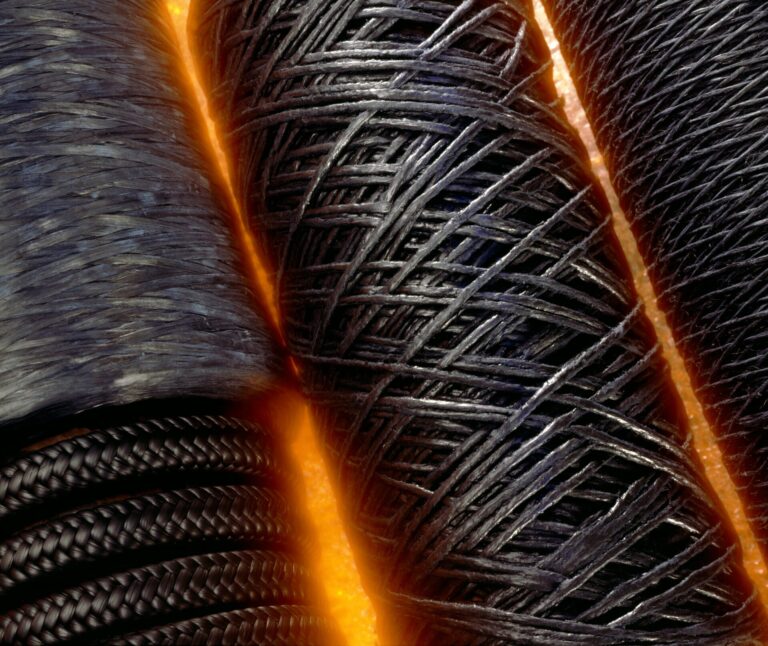
Chemical Engineering
Stronger, lighter, cheaper: a new route to carbon fiber production
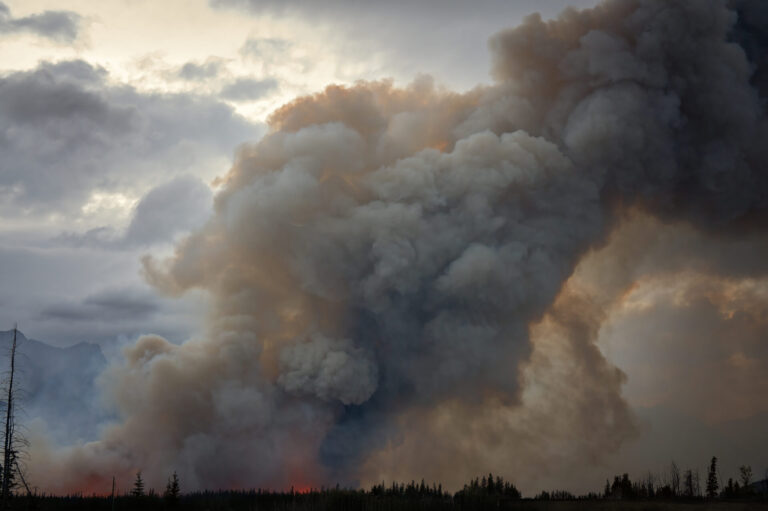
Chemical Engineering
Unveiling the role of biomass-burning aerosols in atmospheric reactions
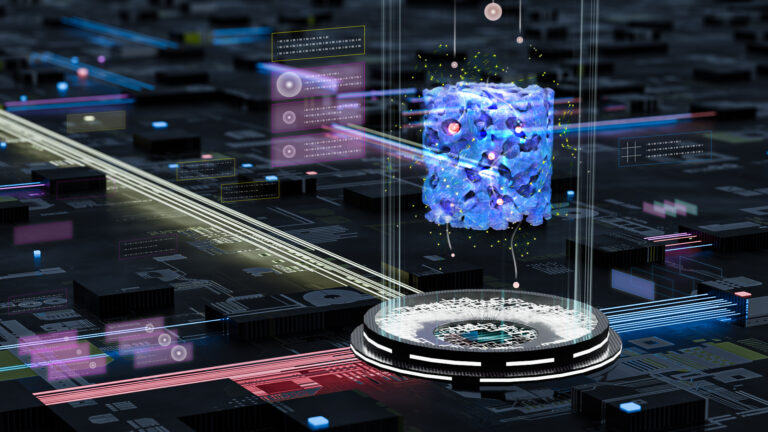
Chemical Engineering
Slashing industrial emissions using a hybrid model approach
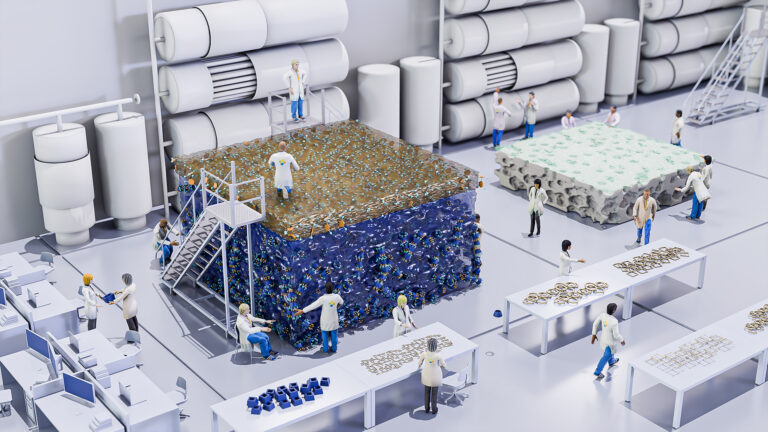
Chemical Engineering
Precision separations with perfect pores
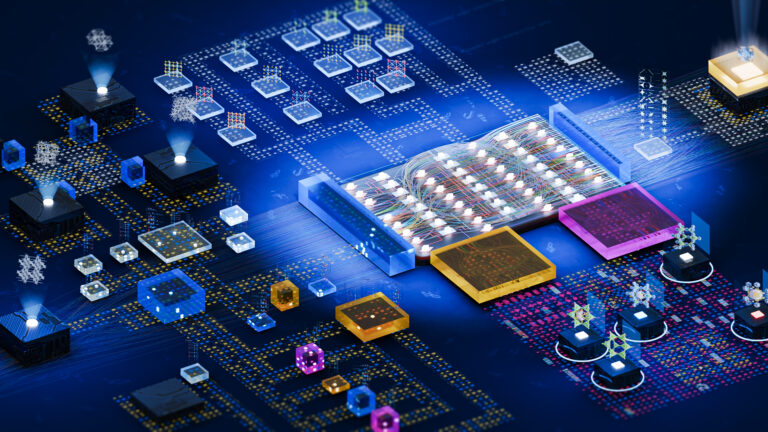
Chemical Engineering
Net benefits for advanced materials design
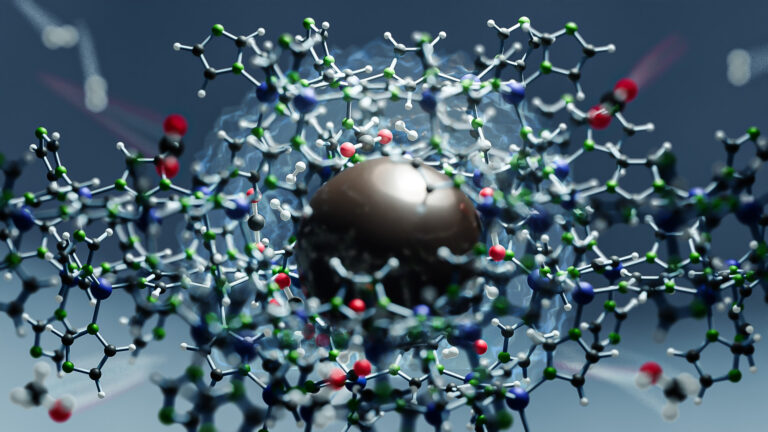
Chemical Engineering