Environmental Science and Engineering
Graphene powers up water purification
Self-cleaning graphene-coated membranes remove water pollutants while harvesting energy from microbial decomposition.
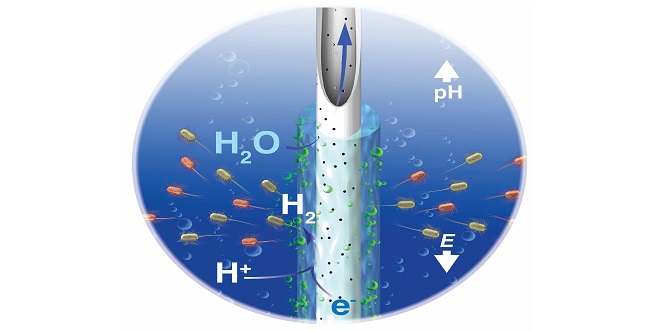
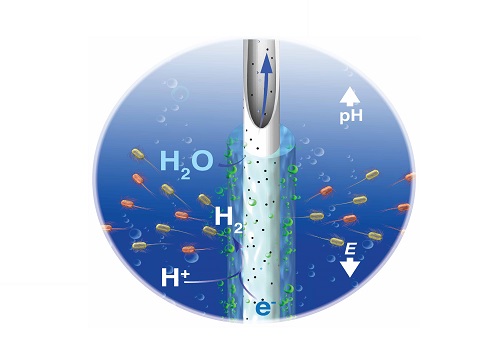
A new wastewater treatment system uses hollow fiber membranes coated with graphene to filter impurities from water and create hydrogen fuel.
© 2016 KAUST
A slight change in membrane layout can have a big impact on reducing biofouling in an advanced wastewater treatment system, a KAUST-led research team1 has found.
Membrane bioreactors (MBRs) have become increasingly popular for wastewater reclamation. MBRs use a mix of bacteria to digest pollutants and porous membranes to separate bio-generated solids from clean water in a single tank. Despite the small footprint of this design, it requires significant energy to aerate the reactor and provide it with oxygen—an ingredient needed for bacterial respiration and to control the sticky “fouling” films that build up on membranes.
Krishna Katuri, Craig Werner and Pascal Saikaly from the University’s Water Desalination and Reuse Center and colleagues from the KAUST Advanced Membranes & Porous Materials Center recently developed an alternative anaerobic electrochemical membrane bioreactor (AnEMBR) that works without oxygen. The device contains special electroactive bacteria that release electrons and protons at the anode when they digest organic matter. By driving electrons and protons to join up into hydrogen gas at a cathode, enough clean-burning fuel is recovered to power the entire treatment process.
To reduce space, the AnEMBR system contains long and porous hollow fibers that act as both catalytic cathodes and filtration membranes. However, the absence of oxygen in this technique made it challenging to control membrane fouling. The team realized that hydrogen bubbles forming on the cathodes could self-scour biofilms off membrane surfaces if gas generation rates were high enough.
“Several features in the reactor design and operation can affect hydrogen production rates and fouling in the AnEMBR system, such as electrode spacing and operating voltages,” says Saikaly. “However, the specific cathode surface area typically limits its performance, making it a key design factor for us.”
The team produced two types of reactor configurations—a rectangular layout where the anode faced opposite the cathode and a tubular shape where the anode was stacked below the graphene membrane. Treatment trials revealed that closely spaced rectangular electrodes produced the highest amount of hydrogen bubbles and significantly delayed membrane biofouling.
To delve deeper into the reactor’s preference for rectangular shapes, the researchers used genomics to analyze any microbes developing on the membrane surfaces. These tools revealed an abundance of methanogens on the tubular reactor that consumed hydrogen gas almost as fast as it was produced. Membranes in the rectangular reactors proved less hospitable to the micro-bugs.
Saikaly notes these findings should help testing of real domestic wastewater by indicating how to optimize electrode configurations for low-conductivity solutions.
References
-
Werner, C. M., Katuri, K. P., Hari, A. R., Chen, W., Lai, Z. Logan, B.E., Amy, G.L. & Saikaly, P.E. Graphene-coated hollow fiber membrane as the cathode in anaerobic electrochemical membrane bioreactors – Effect of configuration and applied voltage on performance and membrane fouling. Environmental Science & Technology 50, 4439-4447 (2015).| article
You might also like
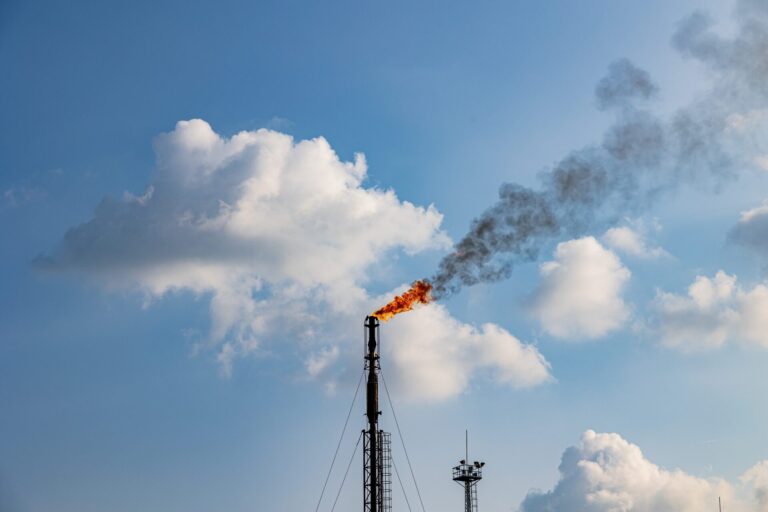
Environmental Science and Engineering
Combat climate change by eliminating easy targets
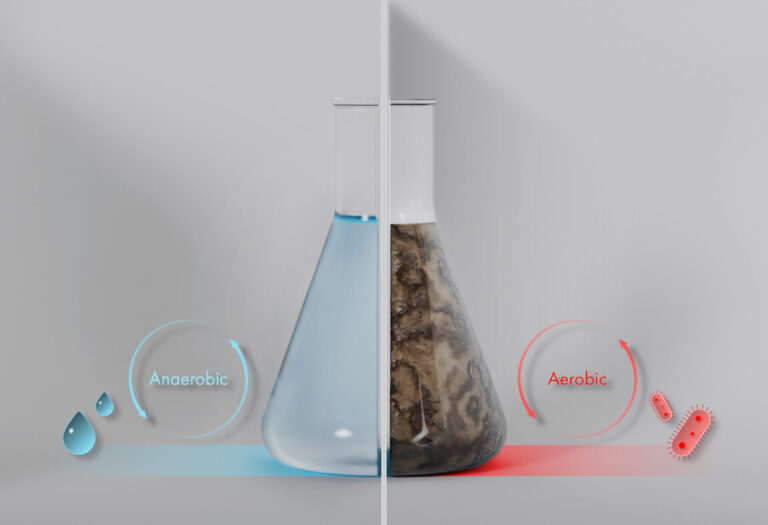
Environmental Science and Engineering
Wastewater treatment to fight the spread of antibiotic resistance
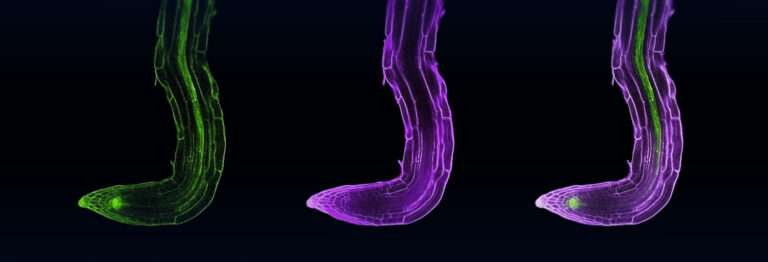
Bioscience
Digging into the world of plant-growth-promoting microbes
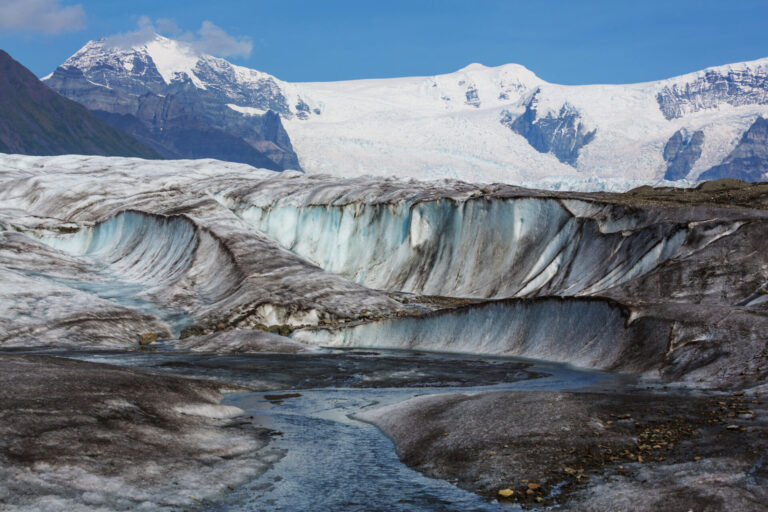
Bioscience
Unique microbiome discovered in mountain streams
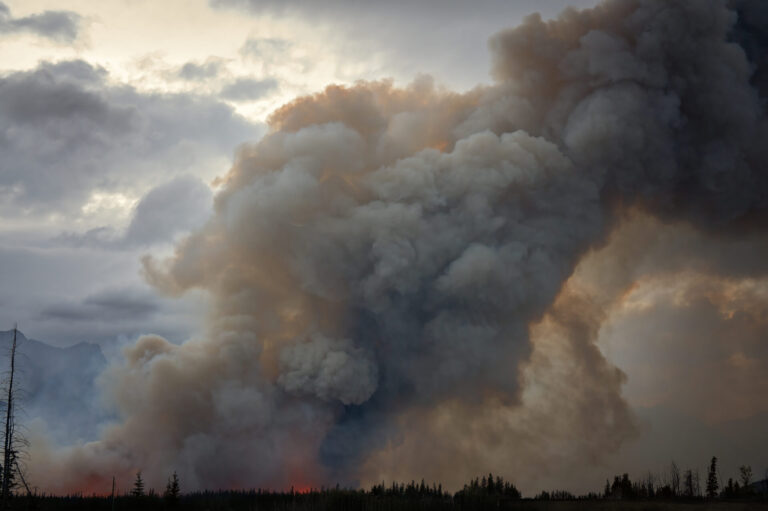
Chemical Engineering
Unveiling the role of biomass-burning aerosols in atmospheric reactions
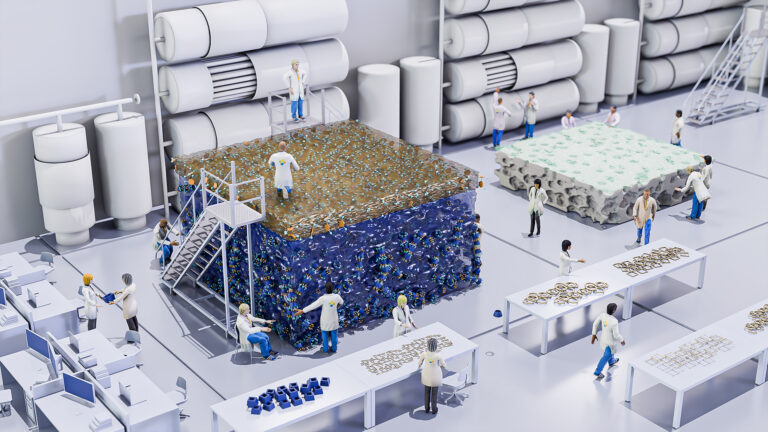
Chemical Engineering
Precision separations with perfect pores
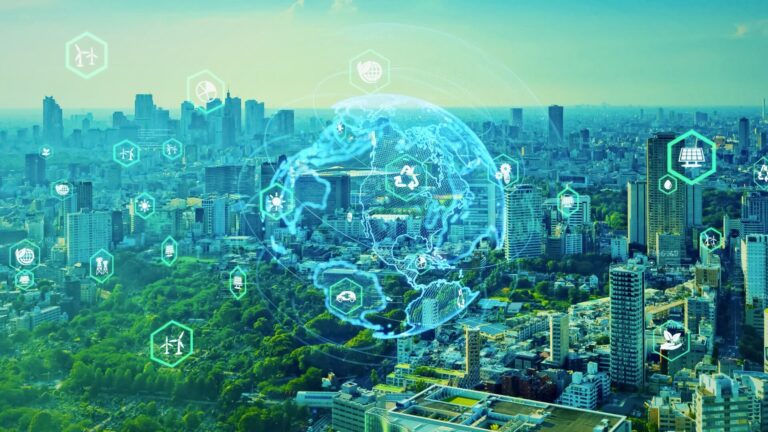
Environmental Science and Engineering
Practical support for building sustainability into our cities
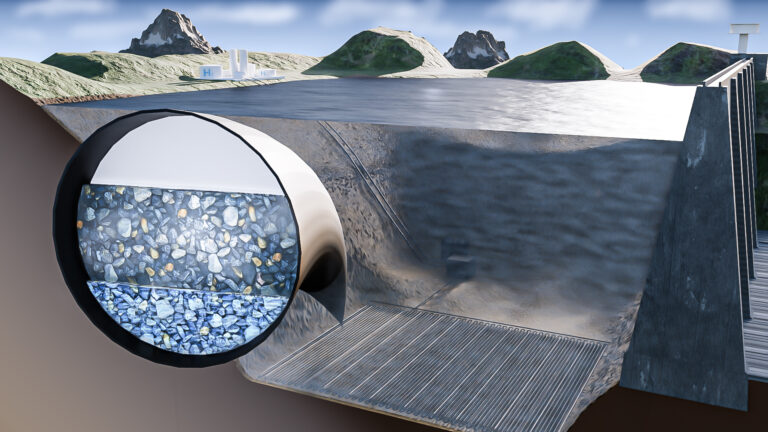
Environmental Science and Engineering