Mechanical Engineering
Making a splash
Ultrafast imaging reveals the influence of even ultrasmall surface roughness on inkjet printing.
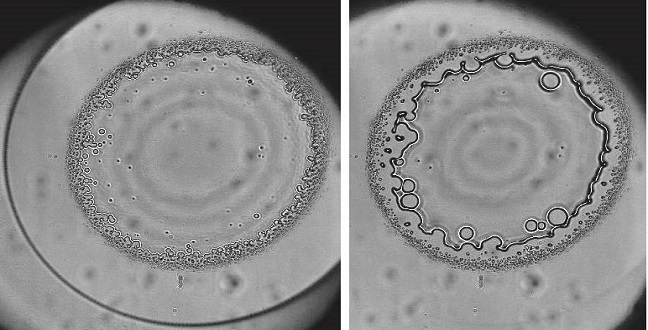
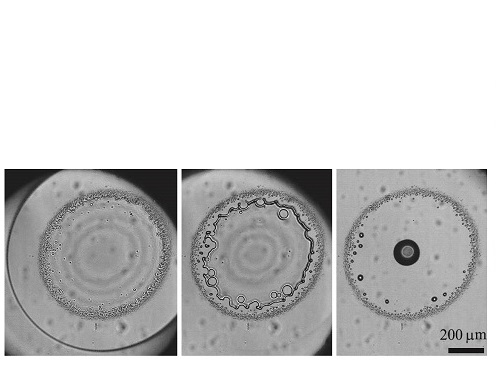
Frames from an ultra-high-speed video show the air bubbles trapped under a water droplet impacting on a glass surface. The imaging is through the glass.
Reproduced with permission from ref 1© 2015 Cambridge University Press.
The impact of drops on a glass surface has been captured at ultrafast time scales by researchers at KAUST. Using a high-speed video camera, the researchers discovered even minute surface roughness leads to the formation of a ring of small microbubbles underneath a droplet1.
“The drop can distinguish between a 10 nanometer glass roughness and perfectly smooth mica. This is quite surprising,” stated Sigurdur Thoroddsen, lead of the research team at the University.
Studying drop dynamics is relevant to applications ranging from inkjet printing to industrial coatings and to the fabrication of mobile phone displays that use printed organic electronic circuits.
The inkjet printing processes are technologically challenging, because the drops hitting the surface experience large deceleration forces equivalent to 300,000 times that of gravity. At such speeds, air is trapped underneath the drops during deposition, and, as the researchers observed, this creates a ring of minuscule bubbles at the fringes of the droplets. The bubbles reduce the uniformity of the deposits and can reduce printing quality.
The researchers studied the formation of the microbubbles using a high-speed camera that can record clips at a rate of five million images per second, or at an imaging resolution of 200 nanoseconds.
The camera is placed underneath the glass and laser beams are used as a flash during exposure. The superfast recording speed necessitates a different laser diode for each individual image frame, requiring an array of 180 separate lasers. The advantage of using laser beams is to provide a depth measurement through interference fringes that are visible in the recorded images.
The camera images show the effect of roughness on the bubble formation with more bubbles formed on rough glass than on smooth. In the extreme limit of mica, which has atomically smooth surfaces, no such ring of micro-bubbles formed during the droplet impact.
Even small surface imperfections leave a clear signature on the bubble distribution. Microbubbles form even on glass surfaces with a roughness of only around 10 nanometers, which is about 500 times smaller than the size of the microbubbles that are created and 500,000 times smaller than the drop, presenting severe problems for numerical simulations.
The evolution of the drops also depends on other parameters, which will be the next area of study, noted Thoroddsen.
“The problem of microbubble formation is greater for drops of higher viscosity, where much a larger number of bubbles are entrained. This is our next target; we would like to see how bubbles are entrained for higher viscosity drops,” he said.
References
- Li, E.Q., Vakarelski, I.U. & Thoroddsen, S.T. Probing the nanoscale: the first contact of an impacting drop. Journal of Fluid Mechanics 785, R2 (2015).| article
You might also like
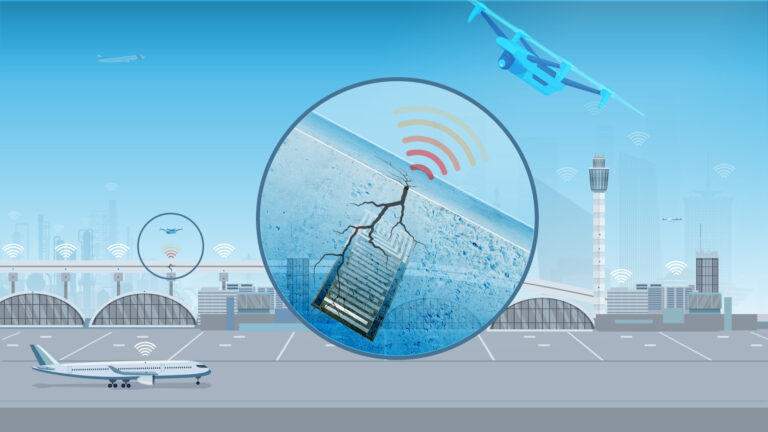
Mechanical Engineering
Innovative strain sensor design enables extreme sensitivity
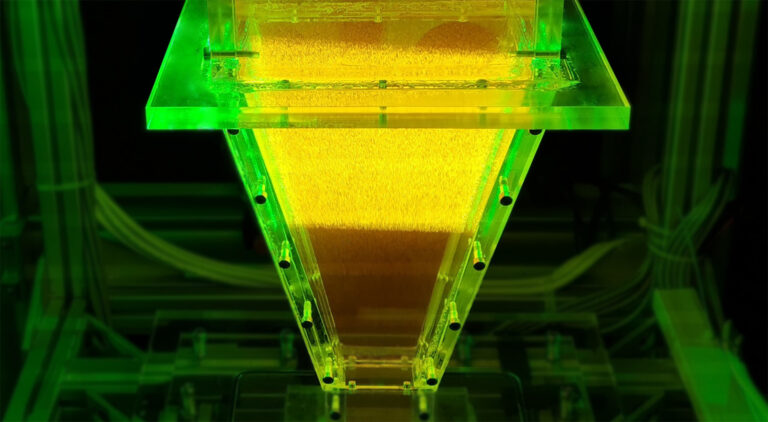
Mechanical Engineering
Turbulent flow shows surprise patterns that could help boost efficiency
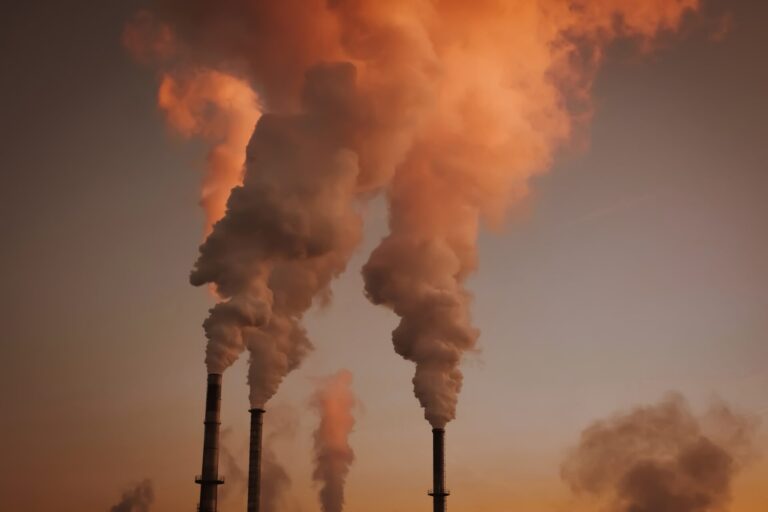
Mechanical Engineering
Machine learning model identifies gas molecules
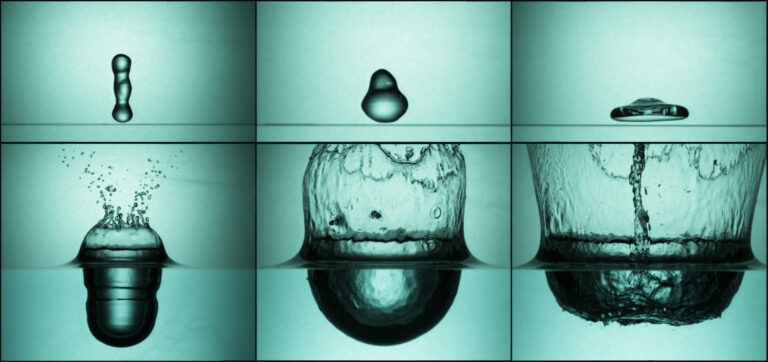
Mechanical Engineering
Making a splash: unraveling the impact of large water droplets
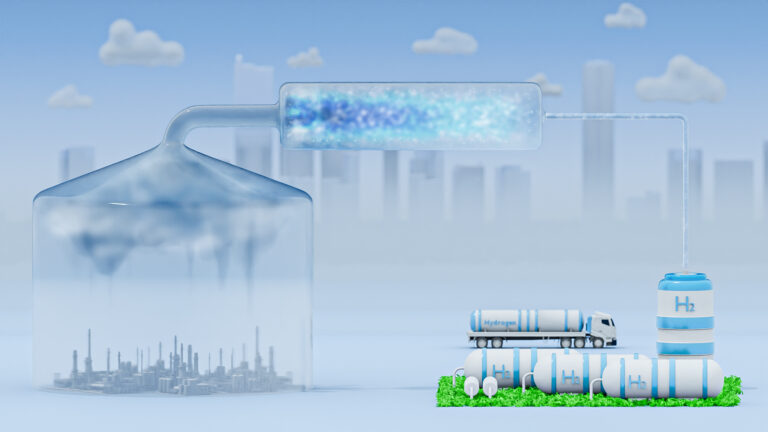
Mechanical Engineering
Sour gas has sweet potential for hydrogen production
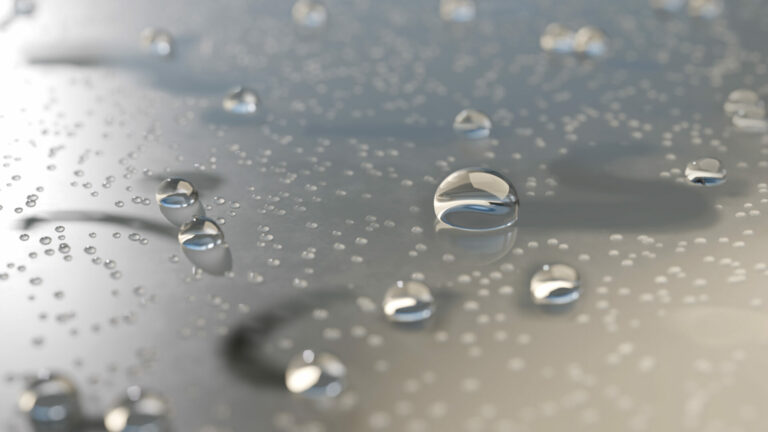
Mechanical Engineering
Dancing droplets’ new spin on water harvesting
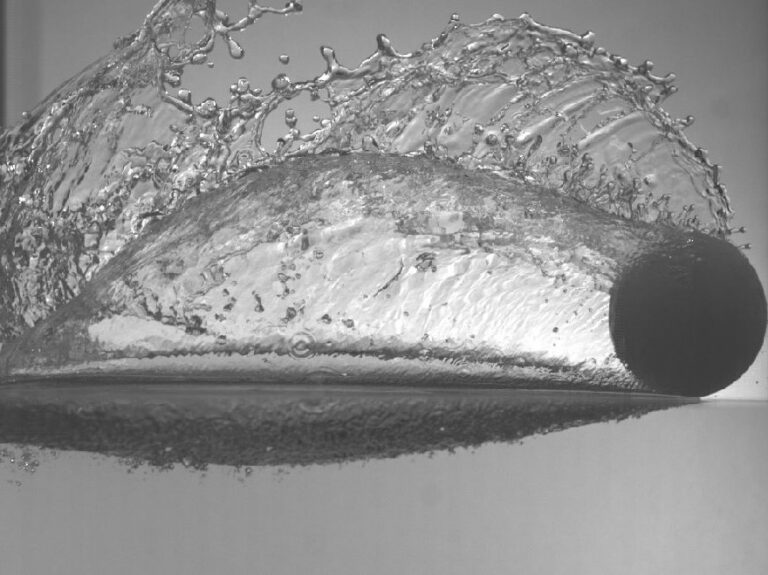
Mechanical Engineering
Underwater air pockets smooth out the bumps
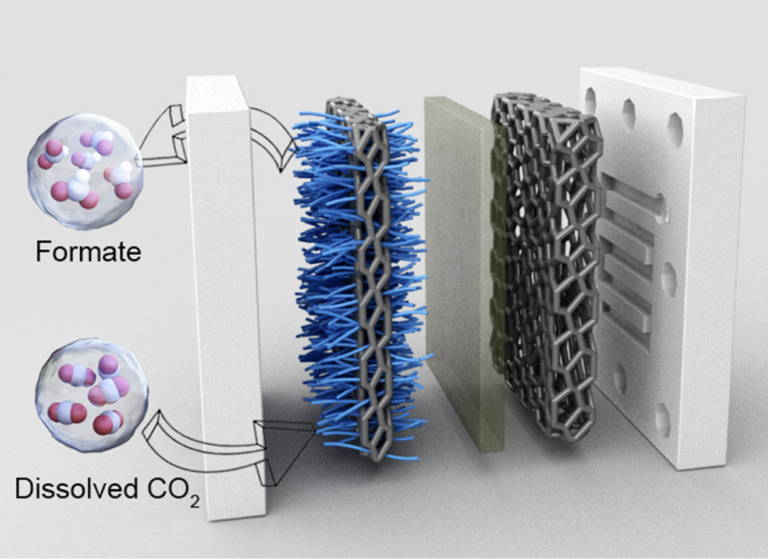
Chemistry