Electrical Engineering
Energy efficiency on a roll
Ultrathin films curve up into long, light and cost-effective heat-harvesting tubes for high-power generation.
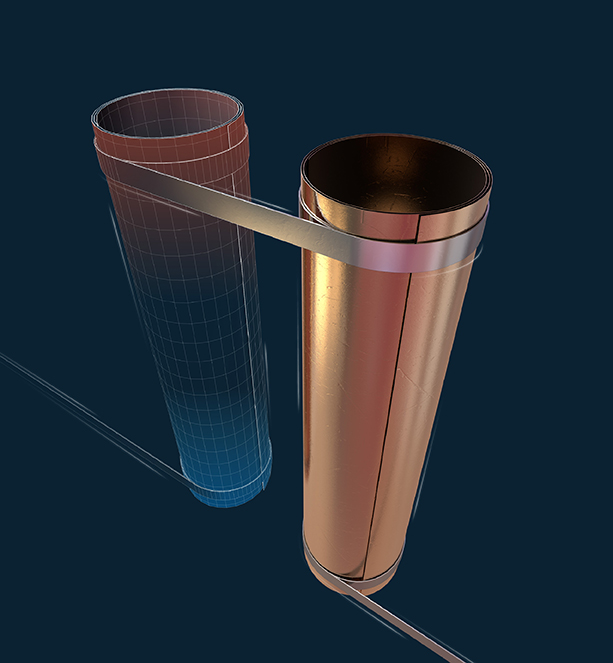
A system that can recycle excess heat into electricity could help meet the increasing energy demands of a growing global population. KAUST researchers have now engineered a lightweight tubular system that can effectively harvest this abundant, clean source of energy that often goes to waste.
“This will help us address the energy crisis and environmental pollution,” says team leader Muhammad Hussain.
Heat is released into the environment by various sources, ranging from industrial machinery to everyday life objects that warm up during operation, such as electronic devices, household appliances and automotive exhaust pipes.
In a concentrated acid solution, the telluride–polymer film lifted off the substrate and spontaneously curled up into a tube.
© 2018 KAUST
Many scientists have attempted to harness this energy source by searching for materials that can create electricity through transforming thermal gradients or temperature differences between hot and cold zones of a system. However, existing thermoelectric materials remain inadequate for high-power generation.
Thermoelectrics hinge on materials that combine high electric conductivity with low thermal conductivity. In these materials, thermal gradients create heat flow, which causes charge carriers to diffuse through the material and produce an electric voltage.
“We are exploring all possible engineering options to augment and maintain the thermal gradient because it directly impacts thermoelectric power generation,” says lead author Devendra Singh. Their team has developed thermoelectric tubular structures of unprecedented length, extending the distance between hot and cold ends and increasing the thermal gradient. The tubes can easily be lengthened for future applications.
By adopting an approach used for sensors, battery technology and cellular vehicle applications, the researchers have invented freestanding thin films that spontaneously roll into seamless tubes under polymer-induced strain. The self-rolling films comprise a stable and easy-to-deposit telluride-containing thermoelectric alloy and a polymer acting as a stress layer.
First, the researchers successively deposited the telluride alloy and polymer layers on a silica-based substrate and consolidated the multilayered architecture by heat treatment. Next, they dissolved the substrate using a concentrated acid solution, causing the telluride–polymer film to lift off and curve up into a tube. “The film rolled upon release because of a stress mismatch between bilayer components,” explains Hussain.
Computer simulations revealed that the tube outperformed solid-rod and flat-slab analogues. Also, it displayed better area efficiency than the slab and competitive advantage compared to the heavier and more expensive rod. A proof-of-concept experiment demonstrated that a tube-based thermopile assembly generated power up to five microwatts for a temperature difference of 60 degrees Celsius.
The team is planning to develop arrays of so-called thermoelectric legs using the self-rolling tubes to optimize power generation.
References
- Singh, D., Kutbee, A. T., Ghoneim, M. T., Hussain, A. M. & Hussain, M. M. Strain-induced rolled thin films for lightweight tubular thermoelectric generators. Advanced Materials Technologies 3, 1700192 (2018).| article
You might also like
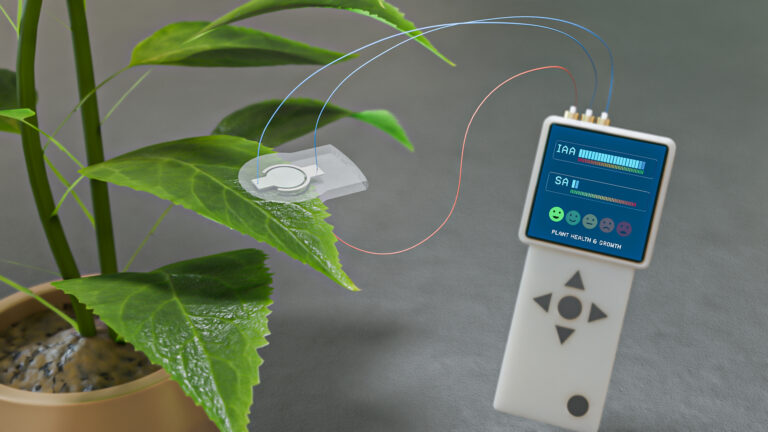
Bioengineering
Sensing stress to keep plants safe
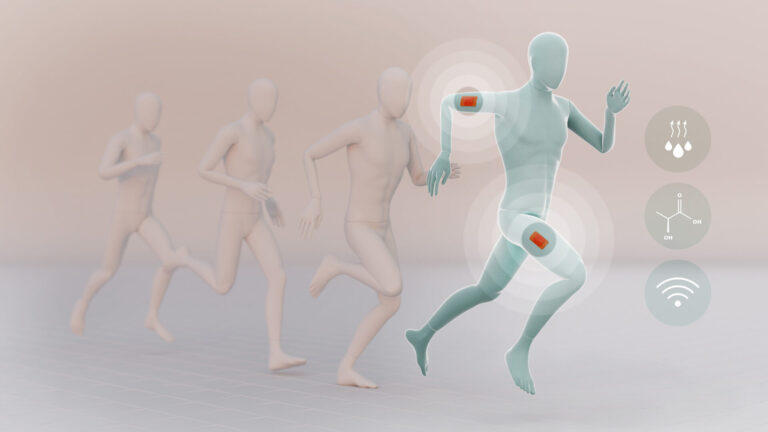
Computer Science
Sweat-sniffing sensor could make workouts smarter
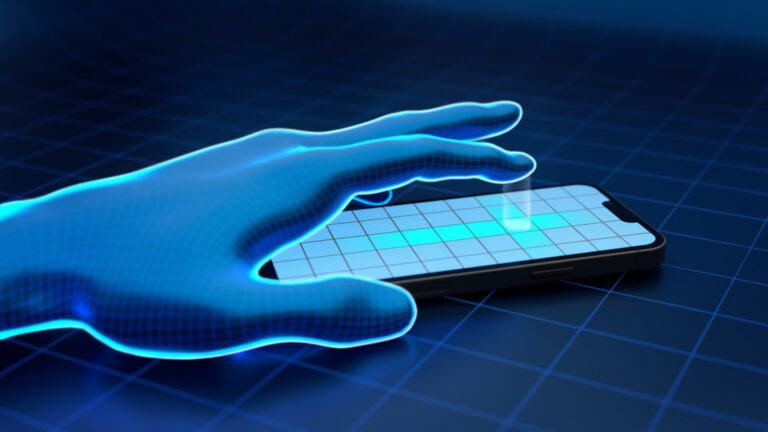
Electrical Engineering
New tech detects dehydration by touching a screen
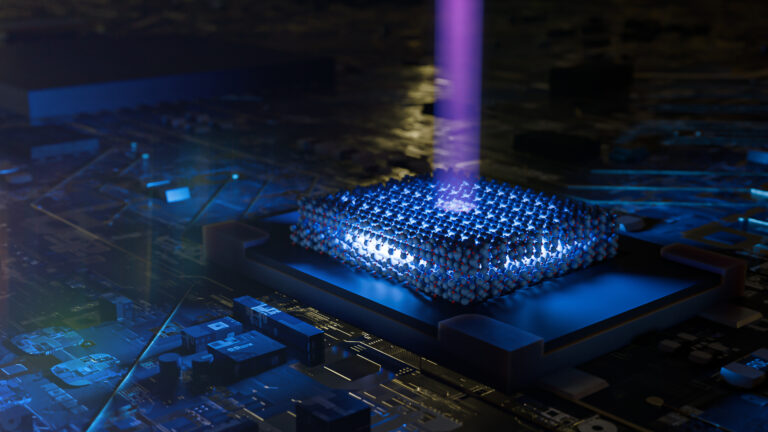
Electrical Engineering
A new interface for efficient electronics

Electrical Engineering
Artificial neurons enable neuromorphic computing with light
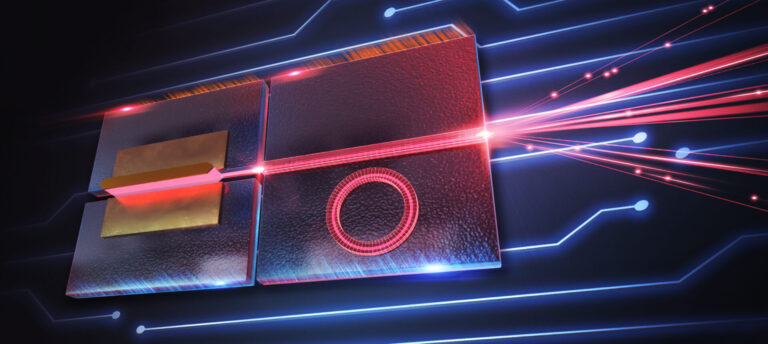
Electrical Engineering
Narrow-linewidth lasers bring low-noise answer
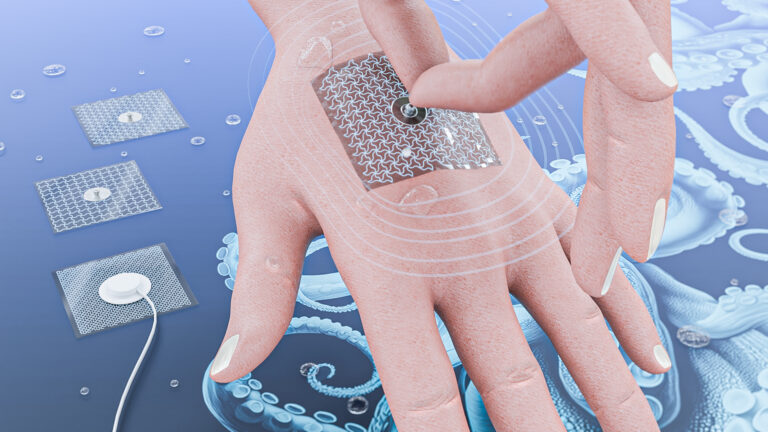
Electrical Engineering
Octopus suckers inspire sticky medical patch
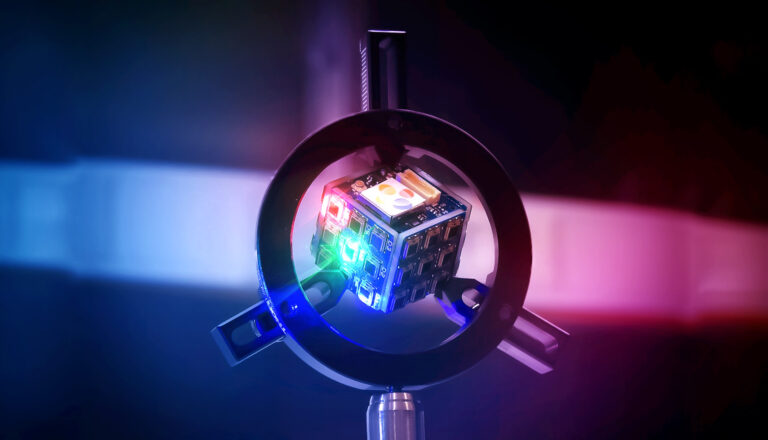
Electrical Engineering