Electrical Engineering
Rolling out an e-sticker revolution
High-speed fabrication developed at KAUST can turn out adhesive and flexible electronic devices in any shape imaginable.
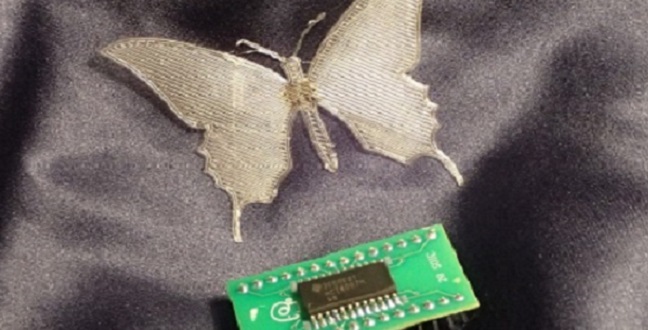
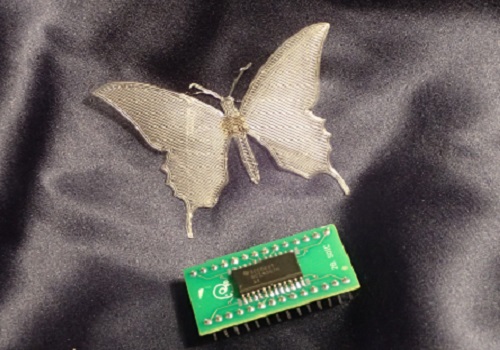
Pressure-sensitive “e-stickers” contain all the functionality of traditional silicon circuits but can be fabricated into complex, flexible shapes such as butterflies.
© 2016 KAUST
The healthcare industry forecasts that our wellbeing in the future will be monitored by wearable wirelessly networked sensors. Manufacturing such devices could become much easier with decal electronics. A KAUST-developed process prints these high-performance silicon-based computers on to soft, sticker-like surfaces that can be attached anywhere1.
Fitting electronics on to the asymmetric contours of human bodies demands a re-think of traditional computer fabrications. One approach is to print circuit patterns on to materials such as polymers or cellulose using liquid ink made from conductive molecules. This technique enables high-speed roll-to-roll assembly of devices and packaging at low costs.
Flexible printed circuits, however, require conventional silicon components to handle applications such as digitizing analog signals. Such rigid modules can create uncomfortable hot spots on the body and increase device weight.
For the past four years, Muhammad Hussain and his team from the KAUST Computer, Electrical and Mathematical Science and Engineering Division have investigated ways to improve the flexibility of silicon materials while retaining their performance.
“We are trying to integrate all device components—sensors, data management electronics, battery, antenna—into a completely compliant system,” explained Hussain. “However, packaging these discrete modules on to soft substrates is extremely difficult.”
Searching for potential electronic skin applications, the researchers developed a sensor containing narrow strips of aluminum foil that changes conductivity at different bending states.
The devices, which could monitor a patient’s breathing patterns or activity levels, feature high-mobility zinc oxide nanotransistors on silicon wafers thinned down lithographically to microscale dimensions for maximum flexibility. Using three-dimensional (3-D) printing techniques, the team encapsulated the silicon chips and foils into a polymer film backed by an adhesive layer.
Hussain and his colleagues found a way to make the e-sticker sensors work in multiple applications. They used inkjet printing to write conductive wiring patterns on to different surfaces, such as paper or clothing. Custom-printed decals were then attached or re-adhered to each location.
“You can place a pressure-sensing decal on a tire to monitor it while driving and then peel it off and place it on your mattress to learn your sleeping patterns,” said Galo Torres Sevilla, first author of the findings and a KAUST Ph.D. graduate.
The robust performance and high-throughput manufacturing potential of decal electronics could launch a number of innovative sensor deployments, noted Hussain.
“I believe that electronics have to be democratized—simple to learn and easy to implement. Electronic decals are a right step in that direction,” Hussain said.
References
- Sevilla, G.A.T., Cordero, M.D., Nassar, J.M., Hanna, A.M., Kutbee, A.T., Arevalo, A. & Hussain, M. M. Decal electronics: Printable packaged with 3D printing high-performance flexible CMOS electronic system. Advanced Materials Technologies 2, 1600175 (2016).| article
You might also like
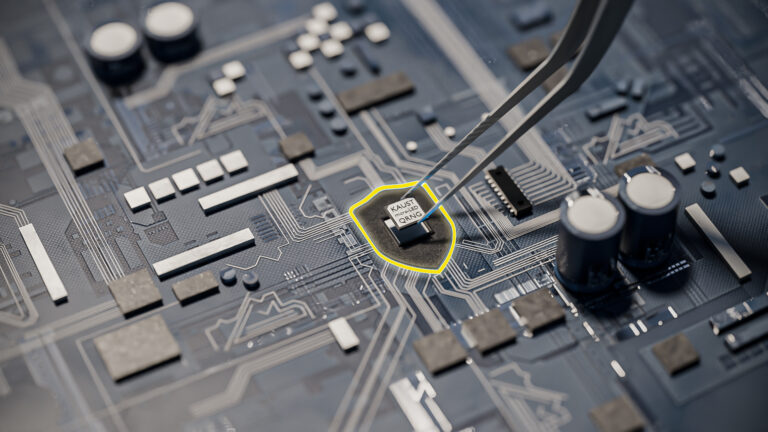
Electrical Engineering
Micro-LEDs boost random number generation
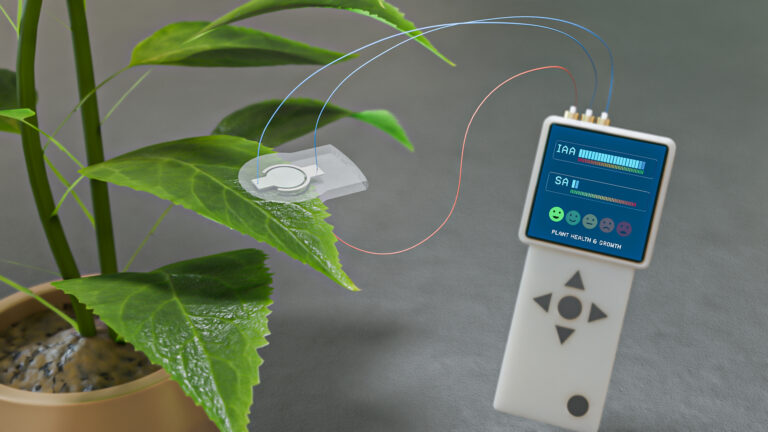
Bioengineering
Sensing stress to keep plants safe
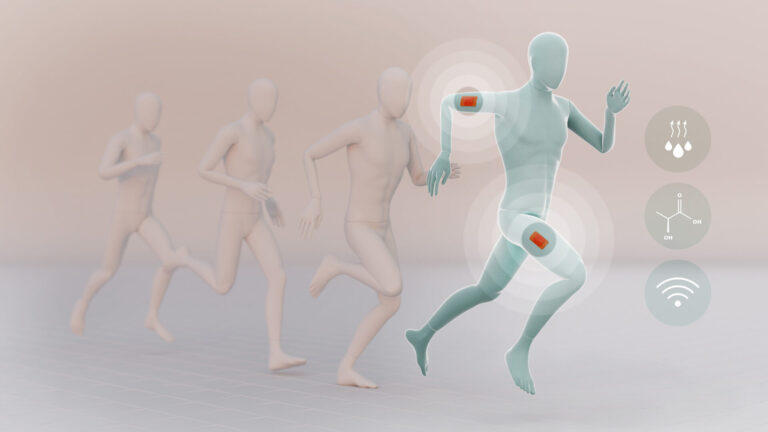
Computer Science
Sweat-sniffing sensor could make workouts smarter
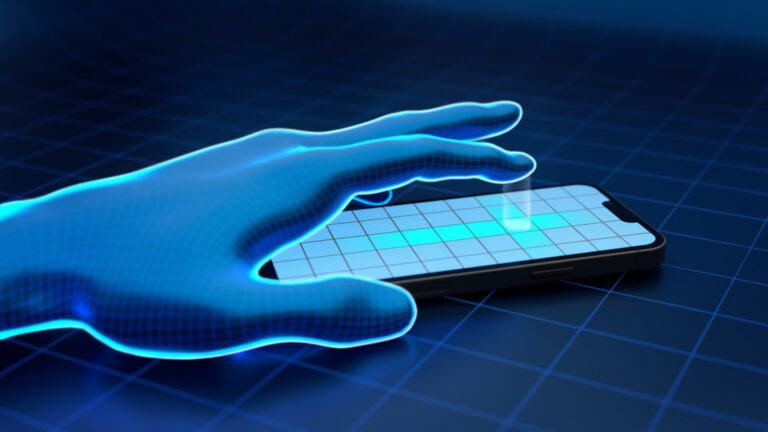
Electrical Engineering
New tech detects dehydration by touching a screen
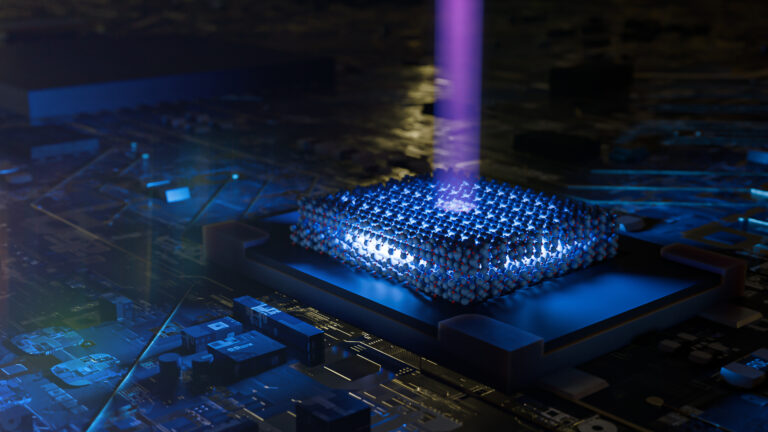
Electrical Engineering
A new interface for efficient electronics

Electrical Engineering
Artificial neurons enable neuromorphic computing with light
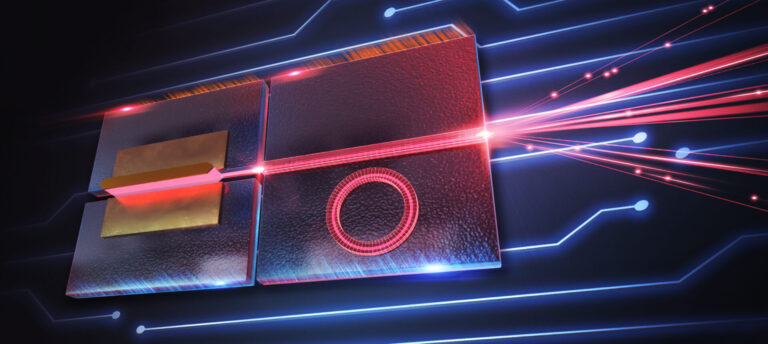
Electrical Engineering
Narrow-linewidth lasers bring low-noise answer
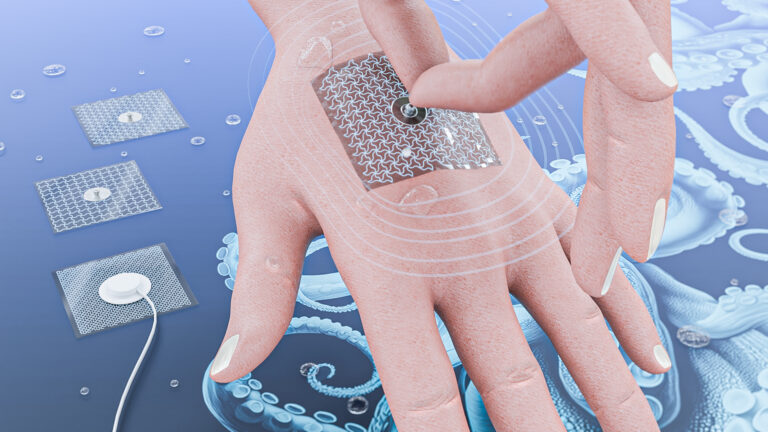
Electrical Engineering